Состав смеси и пропорции для арболитовых блоков
По мере того как технический прогресс двигается вперед, появляются все новые материалы для строительства домов своими руками. Если раньше дело ограничивалось деревом, камнем или кирпичом, то сегодня существуют различные виды бетона, которые превосходят другие материалы по характеристикам. Одним из таких материалов является арболит. Это уникальный материал, который вместил в себе преимущества как бетона, так и древесины. Его состав достаточно прост, и вы можете приготовить раствор своими руками. Примечательно, что он может использоваться как обычный бетон, путем заливки смеси в опалубку, а может быть, сделан в виде блоков, для обычной кладки. Арболитовые блоки можно купить в специализированном магазине, или приготовить раствор своими руками, сделав блоки из готовой смеси.
Все что нужно – знать точный состав арболита, пропорции для смешивания смеси и технологию его приготовления. Давайте рассмотрим все детальней.
Арболитовый блок – из чего он состоит
Арболит, из которого формируют арболитовые блоки для кладки, состоит из 3 основных компонентов:
- заполнитель;
- минеральное вяжущее;
- химические добавки и вода.
Путем соединения всех этих элементов получается арболитовый раствор, который впоследствии используется для формирования блоков. Состав достаточно простой и каждый сможет сделать материал для своих целей. Сам по себе материал легкий, поэтому блоки идеально подходят для кадки. Их достоинством, по сравнению с газоблоками и пеноблоками, является большая граница прочности. Они стойкие к трещинам и ударам.
Несмотря на то что главным компонентом является древесные опилки (щепа), арболит высоко ценится и не уступает по характеристикам традиционным материалам. Наоборот, арболитовые блоки хорошо сохраняют тепло и создают хороший микроклимат в помещении.
Органический заполнитель
Львиную долю в составе арболитных блоков занимает древесная щепа. Это основной материал, который входит в его состав. Такой органический заполнитель легко можно приобрести за небольшие деньги. Стоит обратиться в местную пилораму, где есть отходы деревообработки и договориться с работниками. Преимущественно используют хвойные породы дерева и твердолиственные. Пихта, сосна, ель, осина, бук, береза и тополь идеально подходят, чтобы сделать из них арболитовый раствор. Также можно использовать костру льна.
Чаще всего применяется древесный заполнитель: дробленка, стружка с опилками, в пропорции 1:1 или 1:2, щепа, стружка и опилки, в пропорции 1:1:1. Все пропорции измеряются в объеме. К примеру, если нужно добиться соотношения 1:2, то берется 1 ведро древесных опилок и 2 ведра стружки. Опилки легко заменяются кострой льна или конопляными стеблями, на состав это не повлияет.
Какие требования к заполнителю? Прежде всего, важно правильно подобрать их размер. Крупные опилки использовать не рекомендуется, ведь когда изделия вступят в контакт с водой, они могут увеличиться в объеме. В результате блок может разрушиться. Если же использовать слишком мелкие частицы, то увеличивается расход цементной смеси. Рекомендуемый размер частиц – 15 или 25 мм длинной и не больше 2–5 мм шириной. Сырье не должно иметь листья и другие примеси.
Предупреждение! Лиственница и свежесрубленная древесина любых пород в состав арболитовых растворов не добавляется. Это запрещено!
Костра льна
Полноценным заполнителем, добавляющимся в раствор, является костра льна. Так как в ней присутствует сахар, обязательно применяются химические добавки. Чтобы улучшить качества готовой смеси для блоков, костра заранее обрабатывается известняковым молоком, в пропорции: 200 кг костры на 50 кг извести. Затем все выдерживается несколько дней в куче, после чего все готово для производства арболита. Благодаря такой технологии расход цемента значительно уменьшается. На 1 м3 арболита требуется 50–100 кг цемента.
Важно! Если костра льна используется в обычном виде, то конопляные стебли требуют некой обработки. Их нужно предварительно измельчить.
За счет того, что в составе отходов органики есть вещества, растворимые водой, среди которых смоляные кислоты и сахар, это препятствует хорошей адгезии между частицами. Для устранения сахара, древесные щепки требуется выдержать на воздухе 3 или больше месяцев, или обработать его известняком. Во втором случае смесь выдерживается 3–4 дня. Содержимое перемешивается 2 раза на день.
Минеральное вяжущее
Вам никак не сделать раствор своими руками без вяжущего компонента. Он делает арболитовые блоки прочными и пригодными для кладки. В качестве вяжущего вещества используется портландцемент марки М400, М500 или еще выше.
Его расход зависит от вида заполнителя, крупности частиц, марки цемента, характеристик и т. д. Чтобы немного ориентироваться, можно определить расход таким образом: коэффициент 17 нужно умножить на требуемую марку арболита. К примеру, вам нужно приготовить раствор, маркой 15 (B1). В таком случае на 1 м3 арболита потребуется 255 кг цемента.
Химические добавки
Свойства, которые имеют арболитовые блоки, напрямую зависят от химических добавок. Их использование обязательно в любом случае, неважно, в каком климате выполняются работе. Благодаря добавкам, заполнитель можно использовать без выдержки, ведь они нейтрализуют сахар и другие вещества, что улучшает качество готовых блоков.
В качестве таких добавок может использоваться:
- жидкое стекло (силикат натрия). Закрывает все поры в древесине, поэтому влага не попадет внутрь. Используется после удаления сахара;
- гашеная известь. Она расщепляет сахар и убивает микроорганизмы в опилках;
- сернокислотный алюминий. Отлично расщепляет сахар. Благодаря компоненту состав быстрее набирает прочность;
- хлористый кальций. Убивает все микроорганизмы и придает древесине противогнилостных свойства.
Сернокислотный алюминий и хлористый кальций считаются лучшими добавками. Пропорции добавок – 2–4% от массы цемента, или от 6 до 12 кг на 1 м3. Добавки можно сочетать между собой.
Пропорции для арболитовых блоков
Чтобы сделать арболитовые блоки своими руками важно знать не только состав, но и пропорции. Соотношение всех компонентов между собой следующее: 4:3:3 (вода, древесная щепа, цемент). Химические добавки – 2–4% от общей массы.
Для изготовления 1 м3 арболита своими руками, из которого будут сделаны блоки для кладки, вам потребуется:
- 300 кг древесных отходов;
- 300 кг портландцемента;
- 400 л воды.
В раствор добавляется хлористый кальций или другой химикат. Это классический состав, который легко можно сделать своими руками. Все что потребуется: бетономешалка или большая емкость для размешивания, ведра, лопаты, вилы (для перемешивания вручную) и все компоненты арболита. Процесс выполнения работ следующий:
- Наполнитель (щепу) засыпают в емкость и смачивают водой. Тогда сцепление с цементом будет лучше.
- Затем, постепенно добавляется цемент с добавками. Содержимое тщательно перемешивается в бетономешалке или своими руками, при помощи вил.
- Настало время добавлять воду, в которой уже растворены химические добавки. Все снова перемешивается.
- Как цемент, так и воду требуется добавлять не сразу, а понемногу, небольшими порциями. Так смесь будет легче перемешивать и компоненты будут лучше соединяться между собой.
- После того как сделан раствор, его нужно поместить в подготовленные формочки, чтобы они обрели вид блоков для кладки.
Это состав и пропорции смеси арболитовых блоков, которые можно сделать своими руками. Все что требуется – быть внимательным и четко придерживаться инструкций по его приготовлению. Ниже приводится таблица, которая поможет вам разобраться в том, какие есть марки арболита и каковы пропорции компонентов для его приготовления.
Какой раствор используется для кладки
Это логичный вопрос. Ведь если арболит специфический материал, то может для кладки арболитовых блоков потребуется специфический раствор? Нет. Арболитовые блоки кладутся на обычный цементный раствор, который под силу сделать любому. Он состоит из цемента, песка и воды. Соотношение компонентов – 3:1. Вода добавляется до тех пор, пока раствор не приобретет нужной консистенции. Эта смесь идеально подходит для кладки блоков своими руками.
Итак, зная состав, пропорции и технологию замешивания арболитового раствора, вы можете делать блоки для ваших целей.
Этот материал для строительства объектов различного предназначения применяют более пятидесяти лет. При всей своей популярности арболит имеет положительные и отрицательные свойства. В советское время для строительства жилых домов этот материал использовали редко, отдавая предпочтение натуральной древесине, кирпичной кладке или сборным бетонным конструкциям. Сегодня арболит обрел популярность при сооружении всевозможных объектов.
Краткое описание арболита
Итак, что такое арболит?
Своим названием материал обязан французам. В переводе с их языка это означает «дерево».
Арболит от простого материала отличается методом изготовления. Его укладывают в форму для арболита или опалубочную конструкцию в жидком состоянии. Высыхая, материал получает проектные качества прочности.
Сам арболит и изделия из него должны соответствовать общим техническим условиям, определенным ГОСТом 19222 84 и ГОСТом 54854 2011.
Состав
Второе название – древобетон, для производства которого используют три основных ингредиента:
- Наполнители в виде рисовой соломки, льняного костра, хлопковых стеблей, хвои, древесной щепы или коры. Длина их достигает двадцати пяти сантиметров, ширина – один сантиметр.
- Вяжущие составы в виде цементного материала не ниже М300.
- Стабилизаторы, при помощи которых регулируется улучшенное сцепление щепы, степень затвердевания материала и пластичность. Представлены химдобавки сернокислым алюминием, кальциевым хлоридом либо нитратом, жидким стеклом и т. п.
Больше всего в составе используют древесную стружку, которую иногда заменяют опилками. Качество таких блоков несколько хуже, да и эксплуатационные данные оставляют желать лучшего. Блок получается более плотным и тяжелым, подвержен деформированию. Но есть некоторые достоинства – такая разновидность арболита отличается приемлемой стоимостью.
Ко всем компонентам арболита добавляется вода.
Виды материала
Различают два вида арболита:
- Конструкционный – содержит много цемента, отличается повышенным показателем плотности, достигающей 500 – 800 килограмм на метр кубический. Из этого арболита строят стены.
- Теплоизоляционный – в него добавляют много щепы, от чего плотность не превышает пятисот килограмм на кубометр. Из такого материала возводятся перегородки, в несущей стене его применяют в качестве утеплительного материала.
Выпуск материала налажен в двух формах:
- блочная – изделия отличаются определенными размерами. Гостом установлены не только параметры, но и разрешенные отклонения. В итоге размерная погрешность несколько выше, и это следует учесть во время ведения работ, иначе между блоками получатся швы, отличающиеся между собой по толщине. Блок позволяет максимально сократить строительные сроки, потому что рабочий темп задается только временем, необходимым для застывания раствора;
- монолитная – изготавливается непосредственно на строительной площадке и сразу применяется, так как хранить такой материал невозможно. Больше всего монолитный вариант используется при утеплении. Но известны случаи, когда монолитным способом строили небольшие объекты.
Приготовление монолитного материала удешевляет строительный процесс, только скорость работ снижается. В отличие от остальных разновидностей бетона этому материалу необходимо много времени, чтобы стать прочным.
Технология производства
Изготовление включает несколько рабочих этапов. На автоматической линии для арболита предварительно выполняется дробление стружки, потом – ее сортировка. Чтобы наполнитель состоял из частиц нужного размера, стружку пропускают через сито.
После этого наполнительный компонент обеспыливается. Его смешивают с цементом, химическими компонентами и водой. Подготовленный раствор выливается в формы, изготовленные из металла. Это помогает получить ровные блоки с гладкой поверхностью.
Смесь, залитая по формам, утрамбовывается при помощи вибропресса и выдерживается до полного отвердения. До отправки на строительную площадку блоки просушиваются в течение двух недель, пока не станут достаточно прочными.
А как делают арболит в домашних условиях? Такой процесс тоже подразумевает соблюдение некоторых технологических особенностей.
Формы разрешается сделать из толстых досок, чтобы можно было при необходимости их разобрать.
Если соблюдать рецепт арболита по ГОСТу, то на 1 м3 сырья потребуются следующие пропорции ингредиентов:
- столько же стружки;
- 400 л воды;
- химические добавки в количестве 2 – 4 % от всего веса.
Известны рецептуры, по которым в качестве исходного сырья дополнительно используют:
- жидкое стекло для арболита;
- хлористый кальций для арболита;
- сульфат алюминия для арболита;
- пластификаторы для арболита.
Стружка просеивается, чтобы удалить крупные частицы. Потом ее высыпают в бетоносмеситель, заливают воду, в которой предварительно растворены добавки. Все смешивается, после чего добавляется цемент. Состав, получивший однородность, выкладывается в формы, предварительно смазанные известковым раствором. В момент укладки смесь тщательно трамбуется, чтобы до верхнего края она не доходила сантиметра на два. Оставшийся объем заполняется штукатурной смесью.
Приготовленный по такому рецепту арболит выдерживается в формах минимум сутки, после этого его отправляют под навес на двухнедельную просушку.
Про материал, приготовленный таким способом, есть положительные отзывы. Самодельный арболит отлично подходит для возведения стен и перегородок.
Производители не рекомендуют применять такой материал для обустройства фундаментного основания, потому что несущая способность материала и его устойчивость к воздействию воды оставляют желать лучшего.
Области использования
Материал используют главным образом в частном строительстве для возведения малоэтажных объектов. Из него изготавливаются блоки и панели различных размеров.
За границей такие блоки иногда применяют при строительстве многоэтажных домов и промышленных объектов. Некоторые изготавливают из арболита фундаментное основание, на котором устанавливают стены для гаража или постройки хозяйственного назначения.
Кроме этого, арболитовую смесь используют в качестве теплоизоляторного материала в каркасных постройках. Кроме того, ей заполняют стены при строительстве колодцевых кладок.
Достоинства и недостатки
Как любой строительный материал, древобетон отличается своими положительными и отрицательными качествами. Из-за низкого показателя прочности его не применяют при строительстве высотных зданий, но в качестве утеплительного материала он вполне подходит.
Рассмотрим положительные характеристики материала:
- теплоизоляционный показатель – самая примечательная особенность арболита. Теплопроводность его составляет 0.08 Вт, что значительно лучше, чем у различных бетонов и кирпича;
- арболит считается аккумулирующим материалом, способен сохранять тепло в помещении из древобетона. Резких температурных перепадов не наблюдается;
- степень горючести материала низкая, он считается трудновоспламеняемым, образует минимальное количество дыма. Его смело относят к пожаробезопасным;
- паропроницаемость высокая. Естественно, что у древесины данный показатель выше, но многие потребители при строительстве бани предпочитают именно арболит, а не другие виды каменных материалов. К тому же, для такого объекта учитывается и огнестойкость арболита;
- прочность конструкционного арболита равна В3.5, так что из древобетона строятся объекты, высота которых не превышает трех этажей. Но арболит отлично противостоит нагрузочным воздействиям на растяжение. Это означает, что во время подвижек и усадки фундаментной основы материал не покроется трещинами, самостоятельно компенсируя все смещения;
- морозостойкость зависит от класса материала и варьируется в пределах F25 – 50. Но если морозы сочетаются с сырой погодой, то срок службы арболита существенно сокращается;
- материал отлично пилится, разрезается, неплохо удерживает в себе крепежные элементы. Он действительно считается отличным решением для объектов хозяйственного предназначения. Если не знаете, чем пилить арболит, смело берите в руки обычную ножовку;
- вес арболитового блока небольшой, что позволяет сократить сроки строительных работ;
- поверхность отлично штукатурится, нет необходимости применять сетку;
- прочность материала высокая – М10 – 25. Даже начинает казаться, что в процессе изготовления применяли пресс;
- изделия из арболита отличаются хорошей звукоизоляцией. Такой эффект возможен благодаря тому, что внутри блока имеется огромное количество пустот, образованных щепой древесины. Кстати, такая структура оказывает влияние на продуваемость материала.
Как видите, достоинств много, но имеются и негативные моменты:
- свойства влагопоглощения – не следует использовать материал в строительстве помещений с заведомо высоким содержанием влаги в воздухе. Древобетон впитывает много воды, но удерживать ее не способен. Если блок погрузить в воду, потом достать, то жидкость стечет, а блок подсохнет. Такая особенность позволяет применение арболита для строительства бани, потому что помещение относится к группе постоянно отапливаемых;
- слабая прочность материала, из-за которой его используют в малоэтажном строительстве и в качестве утеплителя;
- долговечность материала – вопрос открытый. Нет еще достаточного количества данных по эксплуатации, да и многое здесь зависит от качественных показателей арболитного сырья. Одним словом, максимальный срок службы арболита не установлен;
- материал арболит, изготовленный по ГОСТу, может сравниться с пенобетоном. Поэтому стоимость его не самая дешевая. Данный фактор определяется еще и автоматизированной технологией производства.
Отзывы
Иван, Минино: мы строим из арболита дом. Материал приобретал у местных поставщиков. Стены выводил сорокасантиметровой толщины, дополнительный утеплитель не применял. Наружные поверхности отделал сайдингом. Плотность материала хорошая, крепеж держится отлично.
Андрей, Саратов: из такого материала построил дачу. Все работы выполнял самостоятельно, блоки оказались довольно легкими. Домик получился в два этажа, стены – по тридцать сантиметров, обложены кирпичом. Меня уверяли, что арболит продувается, но внутри помещений всегда комфортный микроклимат. Стоит ли строить из арболита? Естественно!
Александр, Липецк: из литого арболита строили с братом гараж. Стены не армировали, ворота поставили металлические. Единственное неудобство – материал получал в течение двух месяцев по два кубометра за один раз. Запасайтесь заблаговременно!
Женя, Соснинск: построил дом в два этажа. Думал, что воспользуюсь пенобетоном, но возить его было далековато. Решил воспользоваться заливным арболитом. Сначала переживал, но дому уже более пяти лет – проблем не возникало. Внутри поверхность стен оштукатурил, поклеил обои. Со стороны улицы устроил облицовку сайдинговыми панелями. Теплоизоляционный слой не устанавливал. Решил узнать, как сделать стружку для арболита – попробую самостоятельно изготавливать блоки.
Разбираясь со всеми «за» и «против» по арболиту, можно долго спорить о его экологичности, рассуждать, горит арболит или нет, можно ли строить из арболита зимой.
На вопрос – вреден ли арболит для здоровья, ответим категорично – нет. Многие интересуются, разрешается ли выполнять монтаж арболита зимой. Нежелательно, так как кладочный раствор будет быстро схватываться на морозе. Лучше использовать листовой арболит.
Основные изготовители материала
Среди известных производителей арболита можно выделить «ЭкоДревПродукт», «Арболит Трейд», Велижский домостроительный комбинат, Вологодский завод, предприятия в Ступино, Каменном лесе.
Отличными показателями известны арболитовые блоки «Сибирский», «Лотос», «НН», «Петрович», «Черновский».
как сделать своими руками +Видео изготовления
Состав арболитовых блоков: пропорции, из чего делают? По мере продвижения и развития технического прогресса на строительном рынке появляется все больше разнообразных строительных материалов для возведения дома своими руками. Если ранее выбор был невелик, а именно камень, дерево или кирпич, т о на сегодняшний день есть различные виды бетона, которые по характеристикам намного лучше обычных материалов.
Одним из таких можно назвать арболитовые блоки.
Общие свойства
Этот материал уникален в своем роде, и в нем есть достоинства древесины и бетона. Но интересно то, что состав арболитовых блоков достаточно простой, и такой раствор вы сможете приготовить даже своими руками. Также отметим и то, что его можно использовать как обычный бетон, если залить смесь в опалубку, а можно использовать для кладки, если использовать блоки. Этот материал вы можете приобрести в специализированных магазинах, или же сделать своими руками смесь и залить ее в формы для создания блоков. Единственное, что важно знать – это точный состав, а также технологию приготовления и пропорции. Давайте ознакомимся с этой информацией подробнее.
Из чего состоит арболитовый блок
Арболит, из которого создают блоки для кладки, имеет в своем составе несколько компонентов, но главными из них считается:
Минеральное вяжущее.
- Вода, химические добавки.
- Заполнитель.
При соединении этих элементов вы получите арболитовый раствор, который используют для создания блоков. Как видите, состав простой и любой человек справится с его созданием, чтобы после использовать в своих целях. Сам по себе материал считается легким, и по этой причине для кладки идеально подходят арболитовые блоки. Если сравнивать с пеноблоками и газоблоками, арболитовые материалы намного прочнее, и имеют высокий уровень стойкости к ударам и трещинам.
Несмотря на то, что главный компонент в составе смеси для арболитовых блоков – это щепа (древесные опилки), он высоко ценится и ничуть не хуже по характеристикам, ем традиционные материалы, и даже лучше, так как арболитовые блоки намного лучше сохраняют тепло и помогает создать в помещении отличный микроклимат.
Заполнитель органического происхождения
Из чего делают арболитовые блоки? Большую часть в составе этого материала занимает именно древесная щепа. Этот материал считается основным из тех, которые входят в состав. Этот органический наполнитель вы можете всегда купить, и это не будет дорого. Достаточно лишь обратиться в местную пилораму, где постоянно в больших количествах имеются отходы в виде опилок, и договориться с работниками. Чаще всего для изготовления смеси и блоков используют твердолиственные и хвойные породы дерева. Сосна, пихта, бук, ель, береза, осина и тополь идеально подойдут, чтобы сделать из них арболитовый раствор. Если есть возможность, можно использовать костру льна.
Но чаще всего используют древесный заполнитель – стружка с опилками, дробленка в пропорции 1:1 или 2:1, опилки и стружка в пропорции 1:1:1. Каждая пропорция должна быть измерена в объеме. Например, если нужно соотношение 2:1, возьмите 2 ведра стружек и 1 ведро опилок. Если нет опилок, их можно легко заменит кострой льна или стеблями конопли, и состав от этого не поменяется.
Какие есть требования к заполнителю? Прежде всего, следует правильно подобрать размер. Не рекомендовано использовать крупные опилки, так как при соединении изделий с водой они могут попросту разбухнуть, а конечным итогом будет разрушение блока. Если же перестараться и использовать слишком мелкие частицы, что расход цементного раствора будет увеличен. Оптимальный вариант – это размер частиц от 15 до 25 мм в длину и не больше 5 мм в ширину. В сырье ни в коем случае не должно быть листьев и прочих примесей.
Предупреждение! Свежесрубленная древесина любой породы и лиственница ни в коем случае не должна попасть в состав арболитовых блоков, так как это запрещено!
Льняная костра
Костра льна считается полноценным заполнителем, который можно и нужно добавлять в раствор. Но из-за того, что в ней есть сахар, придется обязательно использовать химические добавки. Для улучшения качества уже приготовленной смеси для блоков, нужно заранее обработать костру известняковым молочком, причем пропорция следующая – 4:1, т.е. если вы возьмете 400 кг костры, на нее понадобиться 100 кг извести. После этого смешанные компоненты нужно выдержать в куче несколько дней, а по прошествии этого промежутка времени можно начинать изготовление арболитовых блоков. Благодаря этой технологии расход цементной смеси будет существенно уменьшен. Так, на 1 м3 арболита требуется от 60 до 100 кг цемента.
Обратите внимание, что если льняную костру можно использовать в обычном виде, то перед использованием стеблей конопли придется их обработать. Перед использованием их обязательно нужно измельчить.
За счет того, что в составе органических отходов есть специальные вещества, которые растворяются в воде (а среди них есть сахар и смоляные кислоты), это будет препятствовать хорошей адгезии между частичками. Чтобы устранить сахар, выдержите древесные щепки на воздухе хотя бы 3 месяца, или проведите обработку известняком. Если вы используете второй вариант, хватит выдерживания сроком в 4 дня. Смесь, которая на выдержке, обязательно должна быть перемешана 2 раза в день.
Минеральное вяжущее
Какие бы компоненты вы ни нашли, при отсутствии минерального вяжущего компонента ничего не получится. Именно этот элемент улучшает состав арболитовых блоков и делает их пригодными для кладки качественными материалами. В роли такого элемента используют портландцемент М400, М500 и других марок, которые выше.
Расход этого компонента во многом зависит от того, какой был выбран заполнитель, а также от размера частиц, марки выбранного вами цемента и характеристик. Для того, чтобы хоть немного в этом разбираться, определите расход следующим образом – умножьте коэффициент 17 на марку арболита. Например, если вы хотите раствор марки 15 (В1), то на 1 м3 арболита вам потребуется 260 кг цемента.
Химические добавки
Во многом свойства, которыми обладают арболитовые блоки, зависят именно от химических добавок. Их нужно обязательно использовать, и исключений нет, отличие лишь в количестве и разновидности. Благодаря таким добавкам можно использовать заполнитель без выдержки, так как они способны нейтрализовать сахар и смолы, что значительно улучшает качество готового блока.
В качестве таких добавок могут быть использованы следующие вещества:
- Силикат натрия (а иначе – жидкое стекло). Он закрывает все поры в дереве, и поэтому влага не будет попадать внутрь. Можно использовать после того, как будет удален сахар.
- Известь гашеная. Она способна расщепить сахар и убить микроорганизмы в опилках.
- Алюминий (сернокислотный). Это еще один компонент, который отлично справляется с задачей расщепления сахара. Благодаря нему состав становится прочным в несколько раз быстрее.
- Хлористый кальций. Он в состоянии убить все микроорганизмы и дает древесины такие же свойства, что и после обработки антисептиками.
Хлористый кальций и алюминий сернокислотный считаются самыми лучшими видами добавок. По пропорции в смесь следует добавить от 2 до 4% добавок от цементной массы, или же от 7 до 12,5 кг/м3. При желании можно сочетать между собой несколько видов добавок.
Состав смеси арболитовых блоков и пропорции
Для того, чтобы сделать своими руками арболитовые блоки, следует знать не только состав, но и пропорции. Все компоненты используются в следующем соотношении – 4:3:3 (вода, щепа древесная, раствор цемента). Химические добавки, как уже упоминали ранее, составляют от 2 до 4 % от общей массы.
Для того, чтобы приготовить 1 м3 арболита собственноручно, а после сделать из него блоки для укладки, вам понадобиться:
- 300 кг отходов древесных.
- 400 литров воды.
- 300 кг портландцемента.
В раствор следует добавить кальций или любой другой химикат. Этот состав считается классическим, так как его легко сделать своими руками и он доказал свою надежность. Для изготовления из приспособлений вам потребуется бетономешалка или же просто большая емкость для смешивания, лопаты, ведра, вилы (если будете перемешивать все вручную) и остальные компоненты арболита.
Этапы выполнения работ таковы:
- Щепу (т.е. наполнитель) засыпьте в емкость и смочите водой. Благодаря этому сцепление с цементом будет намного лучше.
- После этого следует постепенно добавлять добавки и цемент. Тщательно перемешайте содержимое своими руками или в бетономешалке.
- Теперь можно добавлять воду, в которой должны быть заранее растворены все добавки. Снова перемешайте смесь.
- И цемент, и воду следует добавлять понемногу, маленькими порциями. Благодаря этому смесь будет проще перемешивать, и компоненты будут соединяться между собой лучше.
- Когда раствор готов, поместите его в заранее найденные формочки, чтобы он застыл в виде блоков для дальнейшей кладки.
Эти пропорции и состав смеси арболитовых блоков, которую можно без труда сделать своими руками. Все, что от вас потребуется – это быть внимательнее и придерживаться инструкций по приготовлению. Ниже приведена таблица, которая даст возможность еще лучше разобрать в том, какие существуют марки арболита и какие пропорции компонентов следует соблюдать при приготовлении своими руками.
Марка | Цемент | Древесная щепа | ||||
мешков | ведер | лопат | мешков | ведер | лопат | |
5 | 3 | 13 | 37 | 25 | 100 | 300 |
10 | 3,6 | 15 | 43 | 25 | 100 | 300 |
15 | 4 | 17 | 49 | 25 | 100 | 300 |
35 | 5 | 21 | 61 | 25 | 100 | 300 |
50 | 6 | 24 | 73 | 25 | 100 | 300 |
Какой раствор используют для кладки?
Вопрос вполне обоснован. Так как арболит является специфическим материалом, то возможно для кладки таких блоков требуется специфичный раствор? Нет. Блоки из арболита кладут на стандартный раствор цемента, который тоже можно сделать своими руками. Он делается из песка, цемента и воды. В этом случае соотношение компонентов 3:1. Воду следует добавлять до тех пор, пока раствор не получит нужную консистенцию. Такая смесь будет идеальная для укладки блоков.
Достоинства и недостатки
Хотя арболит считается очень хорошим материалом, у него есть некоторые недостатки. Застройщиков может заставить волноваться ряд следующих моментов:
- На строительном рынке много блоков «гаражного» качества. Их сопротивление теплопередаче прочность неизвестны даже производителям. Есть трудности с покупкой в регионах заводской продукции. Выше были описаны самые важные моменты для производства арболитовых блоков.
- Неточная геометрия. Точность геометрии арболитовых блоков хуже, чем у остальных легкобетонных камней для кладки (газобетона, пенобетона). Это особенно характерно для тех, кто делает материал своими руками. Из-за отклонений в размерах может потребоваться увеличение толщины швов до 1,5 см. Это, в свою очередь, повлечет промерзание кладки по шву, увеличенный расход материала и снижение скорости кладки.
Производители советуют использовать при укладке перлитовые теплые растворы, но это будет немного дороже. В последнее время для того, чтобы улучшать геометрию произведенной своими руками продукции используют фрезерование поверхности.
- Нужна защита от прямого действия влаги. Если кладку ничем не защитить, она будет проницаемой для большого напора ветра, но реальных подтверждений нет. Решить эту проблему легко – наносить на поверхность штукатурного покрытия.
- Ограничения при выборе материалов отделки. Чтобы эксплуатация не шла вразрез с нормами, важно сочетать с арболитовой кладкой лишь «дышащие» виды отделки.
Но помимо этого есть масса положительных моментов:
- Экологичность, так как в состав входят минерализаторы, которые не выделяют вредные вещества.
- Высокая паропроницаемость.
- Легкость (вес). Благодаря легкости и упругости не нужно делать мощный и жесткий фундамент. Еще один бонусом можно назвать сейсмостойкость.
- Удобство обработки.
- Простота установки крепежа. В арболит можно вкручивать саморезы и вбивать гвозди так же, как и в дерево.
- Низкий уровень теплопроводности. Благодаря отличному сопротивлению для малоэтажных строительств есть возможность обойтись без дополнительного укрепления и получить однослойную структуру.
- Низкий уровень звукопроницаемости.
- Не требуется армирование. Вы можете отказаться от армирования кладки и установки монолитного пояса, если объект небольшой.
- Биологическая стойкость.
- Материал признан негорючим.
Заключение
Теперь, когда вы знаете состав, пропорции и технологию приготовления арболитового раствора, вы без труда справитесь с изготовлением блоков для ваших нужд. Это отличный материал для строительства, и он обладает массой преимуществ, которые с лихвой покрывают несколько несущественных недостатков.
Арболит в большинстве источников описывается, как материал, обладающий чудесными свойствами. Рекламные статьи превозносят арболитовые блоки, недостатки материала скромно умалчиваются. Но чудес не бывает, недостатки тоже есть. Чтобы по максимуму использовать положительные качества и нивелировать отрицательные, стоит хорошенько разобраться со свойствами арболита, его характеристиками и особенностями применения.
Состав и производство арболиттовых блоков
Начнем наш материал именно с состава и процесса производства. Все дело в том, что от качества выполнения определенных процессов зависит наличие или отсутствие определенных недостатков материала. А это является очень важным. Арболит позиционируется, как одна из разновидностей крупноячеистых легких бетонов. В качестве наполнителя в нем используется древесная щепа. Щепа связывается в монолитную структуру цементным тестом.
Материал используется в строительстве в нескольких видах:
- крупноформатные кладочные блоки;
- пустотелые блоки;
- теплоизоляционные плиты;
- смеси для заливки ограждающих конструкций по месту.
Кладочные блоки нашли наиболее широкое применение и под понятием «арболит» понимаются, прежде всего, они. Самым распространенным размером арболитовых блоков является 500×300×200 мм. Но в последние время производители стали расширять свои производственные линейки и предлагают арболит в других типоразмерах.
Технология изготовления блоков относительно проста, но как и везде, имеются свои тонкости. Качество будущих изделий зависит от соблюдения нескольких важных производственных моментов. Если производитель использует в наименовании своей продукции термин «арболит», он должен соблюдать требования нормативной документации на такие изделия, это:
- 1. ГОСТ 19222-84 «Арболит и изделия из него. Общие технические условия».
- 2. СН 549-82 «Инструкция по проектированию, изготовлению и применению конструкций и изделий из арболита».
Состав арболитовых блоков
Для изготовления арболитовых блоков используется:
- Древесная щепа;
- Химические добавки;
- Вода;
- Цемент.
#1. Древесная щепа. Итоговая прочность сильно зависит от калибра щепы. Чтобы на выходе был именно арболит, свойства которого строго нормированы, для производства должна использоваться именно щепа. Ее размеры регламентированы. ГОСТ рекомендует максимальный размер частиц 40×10×5 мм (длина/ширина/толщина).
Наилучшие показатели у блоков с размерами щепы из интервалов:
- длина – до 25 мм;
- ширина – 5..10 мм;
- толщина – 3..5 мм.
Опилки, стружки, тырса, костра, солома и все остальное, что пытаются смешивать с цементом для производства арболита, для его изготовления не подходит. Только чистая щепа без коры, листьев, грунта и прочих нежелательных примесей. Считается, что добавление до 10 % коры или 5 % листвы не оказывает серьезного влияния на характеристики арболита. Но лучше когда эти примеси отсутствуют.
Зачастую производства арболитовых блоков, организованы при лесопилках и других деревоперерабатывающих предприятиях. Для них арболит не является профильным направлением. В результате недобросовестные производители, для увеличения рентабельности производства, кроме самой щепы добавляют то, что имеется. Отсюда непредсказуемое качество продукции.
На специализированных предприятиях устанавливают производительные валковые дробилки, откалиброванные под нужный размер щепы.
Для конечного потребителя не имеет большого значения сорт древесины, из которой производится сырье, но технологи должны это учитывать для правильной дозировки минерализаторов и выбора степени уплотнения. Так, щепа лиственницы требует двойного количества добавок относительно других хвойных пород. Чаще других на производство щепы идут сосна, ель, реже лиственные породы.
#2. Химические добавки. Древесный наполнитель содержит сахара, которые препятствуют качественной адгезии цементного теста с поверхностью частичек дерева.
Для решения этой проблемы применяются 2 основные стратегии:
- 1. Высушивание древесного сырья до применения в производстве в течение нескольких месяцев.
- 2. Минерализация поверхности щепы в растворе химических компонентов.
Наилучшие результаты достигаются при комплексном подходе к решению задачи. Снижение содержания сахаров и минерализация сырья позволяет решить и другие важные задачи:
- повышение биологической стойкости материала;
- снижение водопроницаемости при эксплуатации готового изделия.
Для решения всех этих задач, при производстве арболита могут использоваться следующие компоненты: хлорид кальция (ГОСТ 450–77), жидкое стекло (ГОСТ 13078–67), силикат-глыба (ГОСТ 13079–67), сернокислый глинозем (ГОСТ 5155–74), известь (ГОСТ 9179–77).
#3. Вода. Получать арболитовые блоки, характеристики которых соответствуют заданным, можно, следуя определенному порядку технологических операций. Вода с добавлением минерализаторов готовится заранее. Расход компонентов принимается в следующих соотношениях:
Добавка | CaCl2 | Al2(SO4)3 | Al2(SO4)3+ Ca(OH)2 |
---|---|---|---|
Расход на 1м3 арболита, кг | 12 | 12 | 8+4 |
Щепа засыпается в смеситель принудительного действия. Обычные гравитационные бетономешалки не обеспечивают достаточной гомогенизации. Вода с растворенным минерализатором перемешивается и равномерно распределяется по поверхности щепы. Перемешивание происходит на протяжении 20 секунд. На следующей стадии происходит добавление цемента. Перемешивание с цементом длится 3 минуты.
#4.Цемент. Достаточная для применения в строительстве прочность материала достигается только при применении цемента с маркой не ниже 400. Цемент имеет свойство быстро терять марку при хранении. Даже на выходе с завода цемент часто не соответствует заявленным характеристикам. Поэтому лучше когда, арболитовые блоки, технические характеристики которых должны соответствовать требованиям, предъявляемым к конструкционным материалам, изготавливаются из 500-го цемента.
Формование блоков
Формование необходимо завершить в течении ближайших 15 минут после перемешивания. В зависимости от степени механизации последующих процессов различают следующие способы формования:
- ручное формование без вибрирования;
- ручное формование с вибрированием;
- производство на вибростанке;
- производство на вибростанке с пригрузом.
Механизация процессов позволяет получать более высокие по качеству и стабильные по параметрам арболитовые блоки. При этом размеры, геометрия и плотность сохраняются от изделия к изделию.
Выдерживание изделия в опалубке применяют при кустарном производстве, когда снятию опалубки сразу после формования препятствует слишком жидкая консистенция раствора. В общем случае формы снимают без выдержки.
Сырые блоки остаются на съемном днище-поддоне или прямо на полу цеха.
Арболитовые блоки, состав которых одинаков, могут получать различные характеристики в зависимости от способа и степени их уплотнения. Основной целью прессования смеси в форме не является повышение ее плотности. Главная задача – это создание равномерно распределенной по объему структуры из произвольно ориентированной, полностью укрытой цементным тестом, щепы.
Вибрация при уплотнении применяется очень дозировано. Чрезмерное вибрирование приводит к осаждению цементного теста на дне формы. Важно сохранять его равномерное распределение по объему с полным укрытием зерен наполнителя. Даже в арболите высокой плотности щепа не плавает в растворе цемента с водой. Цементное тесто работает, как клей, покрывающий зерна наполнителя. Меняется только концентрация щепы в объеме и толщина покрывающего ее цементного камня.
Уплотнение блоков производится на значения, достаточные для взаимной переориентации зерен наполнителя и увеличения площади их соприкосновения. Сжатия и деформации самой щепы не происходит. Это обеспечивает сохранение размеров блока после снятия уплотняющего усилия.
Необходимость точной дозировки всех компонентов и соблюдения технологии
Точность дозирования компонентов регламентируется ГОСТом. Допустимые отклонения не могут превышать нескольких процентов. В условиях недостатка воды не происходит гидратация всего объема цемента. Ее избыток нежелателен по нескольким причинам:
- Превышение водоцементного соотношения снижает прочность.
- Избыточная пластичность препятствует выниманию сырого блока из формы непосредственно после формования.
- Увеличивается время хранения блока на поддоне до первичного схватывания.
Концентрация минерализаторов щепы, идущей в арболит, важна для прочности и долговечности материала. Дозировки компонентов, приводимые в нормативах, рассчитаны на определенный калибр заполнителя и его влажность на уровне 25 %. Оптимальную дозировку подбирают опытным путем на основе испытаний готовых образцов.
Для протекания процесса гидратации важна температура раствора воды с минерализаторами. Она не должна быть меньше 15 °С. Для набора необходимой температуры в холодное время года воду подогревают или выдерживают в отапливаемом помещении. Возможен также химический нагрев воды при применении в качестве минерализатора CaCl2.
Плотность арболита
По назначению материал условно делят на 2 типа:
- теплоизоляционный;
- конструкционный.
Определяющим фактором является плотность изделия. Считается, что блоки с плотностью до 500 кг/м3 не подходят для использования в составе несущих конструкций. Но они могут применяться для теплоизоляции при возведении наружных стен в строениях, где нагрузка от кровли или перекрытий воспринимается колонами или другими элементами.
Типичными для конструкционных блоков являются значения плотности из интервала от 550 до 700 кг/м3. Но можно купить изделия и с плотностью до 850 кг/м3. Слишком высокие величины указывают на хорошую несущую способность элементов, но уступают более легким в теплоизоляционных качествах. Плотность материала замеряется при установившейся массе, когда блок прекращает терять влагу.
Стены из литого арболита могут иметь плотность порядка 300 кг/м3, но по несущей способности не уступают сложенным из камней с плотностью 550 кг/м3.
Прочность арболитовых блоков
Несущая способность блоков характеризуется их прочностью на сжатие. По результатам испытаний изделиям может присваиваться марка и класс по прочности на сжатие. В общем случае они связаны с плотностью материалов.
Плотность, кг/м3 | Марка | Класс |
---|---|---|
400 — 500 | М 5 | В 0,35 |
450 — 500 | М 10 | В 0,75 |
500 | М 15 | В 1,0 |
500 — 650 | — | В 1,5 |
500 — 700 | М 25 | В 2,0 |
600 — 750 | М 35 | В 2,5 |
700 — 850 | М 50 | В 3,5 |
Как и в случае изделий из тяжелого бетона, марка является средней величиной по результатам испытаний партии образцов. Класс характеризует гарантированную прочность, 95 % образцов должны соответствовать по классности.
Для реальных испытаний с хорошей выборкой зависимость между маркой и классом через переводные коэффициенты не является корректной. В этом случае разрыв между маркой и классом может рассказать о культуре производства на предприятии. Чем меньше разрыв, тем выше организация производства. В отечественной практике изготовления арболитовых блоков это учитывается с помощью коэффициентов вариации. Для изделий 1-ой категории качества допускается значение 18 %, для высшей – 15 %.
В кирпичной кладке мелкий размер изделий делает понятие классности бессмысленным. При покупке крупных кладочных камней, каковыми и являются арболитовые блоки, стоит отдавать предпочтение изделиям с присвоенным классом.
Для возведения несущих стен одноэтажных зданий высотой до 3 м допускается использовать блоки класса от B 1.0. Для более высоких стен нужны элементы класса от B 1.5. Для 2-х — 3-х этажных строений используют блоки классов B 2.0 и B 2.5.
Прочность арболита на сжатие типична для ячеистых бетонов. Важным отличием является прочность блоков на изгиб, которая составляет от 0,7 до 1,0 МПа. Модуль упругости элементов может доходить до 2300 МПа. Такие величины делают арболит особенным среди ячеистых бетонов. Если для пенобетона и газобетона велика вероятность трещинообразования, то для арболита такая проблема не стоит.
Читайте также:
Теплопроводность арболита
Теплопроводность для арболита является одним из ключевых параметров.
Она растет с увеличением его плотности в следующей прогрессии:
Рекомендованная ГОСТом толщина ограждающих конструкций из арболита в умеренных широтах составляет 38 см. Но стены такой толщины возводятся редко. На практике для стен жилых домов блоки 500×300×200 мм кладут плашмя в один ряд. Вместе с внутренней и наружной отделкой этого достаточно для поддержания комфортной температуры в помещениях без появления проблем с выпадением конденсата.
Дополнительная теплоизоляция часто выполняется с помощью теплых штукатурных систем толщиной 1,5-2 см с добавкой перлита. Для не отапливаемых или периодически отапливаемых помещений (бани) нередко применяют кладку блоков на ребро.
Влагопоглощение арболита
В характеристиках арболита указывают величину водопоглощения до 85 % для теплоизоляционных блоков и до 75 % для конструкционных. Эти значения требуют осмысления. Структура блока представляет собой склеенные цементным камнем разрозненные зерна щепы. Они ориентированы относительно друг друга случайным образом.
Вода, наливаемая на поверхность блока, свободно протекает сквозь него. Естественно, что при окунании вода способна вытеснить большой объем содержащегося внутри блока воздуха. Если блок вытащить из воды, вода вытекает, а цементный камень быстро высыхает.
Арболитовые блоки находящиеся в естественной среде, например в стене дома, фактически не накапливают в себе влагу из окружающего воздуха. Это происходит благодаря очень низкой сорбционной влажности материала, т. к. минерализованные щепа и цемент являются негигроскопичными и слабо смачивающимися материалами. Именно это стало причиной популярности использования материала для строительства бань.
Если поливать ничем не закрытую стену из арболита с внешней стороны водой, есть вероятность увидеть ее и внутри. Поэтому материал не используют без фасадной отделки. Для арболита рекомендуют отделку штукатурными растворами или устройство навесных фасадных систем.
Морозостойкость
Постепенное разрушение изделий при замораживании и размораживании происходит в результате расширения замерзающей в пустотах воды. Чем больше воды в них содержится, тем меньше циклов замораживания — размораживания способен выдержать материал без разрушения.
Низкое сорбционное влагопоглощение дает арболиту хорошую стойкость к промерзанию. Минимальное значение составляет F25 и доходит до F50. Защита арболита от прямого воздействия влаги, позволяет повысить реальную морозостойкость материала в конструкции. Кроме этого существуют реальные примеры эксплуатации зданий из арболита на протяжении 7 — 10 лет без повреждений для стен. Причем речь идет о стенах, которые ни чем не защищены от воздействия внешних факторов среды.
Усадка материала
Считается, что арболит совершенно не подвержен усадке. Но небольшие усадочные процессы в первые месяцы все же присутствуют. В основном они прекращаются еще на этапе созревания блока на производстве. Некритичное уменьшение размеров блока (на 0,4 — 0,8 %) возможно уже после укладки блоков в конструкцию.
Некоторое сокращение высоты блоков может происходить и под весом вышележащих элементов, перекрытий и конструкций кровли. Для предотвращения проблем с отделкой не рекомендуется выполнять штукатурные работы в первые 4 месяца после завершения основного комплекса работ.
Огнестойкость арболитовых блоков
По огнестойкости арболитовые блоки имеют следующие параметры:
- группа горючести — Г1, т. е. это трудногорючий материал;
- группа воспламеняемости — В1, трудновоспламеняемый материал;
- по дымообразующей способности — Д1, малодымообразующий материал.
Звукоизоляция
По шумапоглощению арболитовые блоки превосходят такие материалы как кирпич и древесина. Коэффициент шумапоглощения арболитовых блоков составляет 0,17 — 0,6 в акустическом диапазоне от 135 до 2000 Гц.
Паропроницаемость
Арболит это дышащий материал степень его паропроницаемости составляет до 35 %. Именно поэтому в домах построенных из данного материала не бывает сырости, а микроклимат кофортный как в холодное так и в теплое время года.
Недостатки арболитовых блоков
Как бы ни был хорош арболит, недостатки материала все же стоит знать и учитывать.
Поколебать решимость застройщика способны несколько сомнительных моментов:
— 1. Обилие на рынке блоков «гаражного» качества.
Их прочность, сопротивление теплопередаче неведомы даже производителю. Имеются трудности с приобретением заводского арболита в регионах. Выше мы писали про самые важные моменты производства арболитовых блоков. Как вы понимаете выполнить определенные задачи в кустарных условиях просто не возможно.
— 2. Недостаточная точность геометрии.
Точность геометрии арболитовых блоков уступает таковой у других легкобетонных кладочных камней (пенобетона, газобетона). Особенно это характерно для производств с большой долей ручного труда. Отклонения в размерах и взаимном расположении поверхностей заставляют увеличивать толщину швов до 10 — 15 мм. А это влечет промерзание кладки по швам, перерасход материала и снижение скорости кладочных работ.
Производители рекомендуют использовать для кладки теплые перлитовые растворы, но их приготовление обходится дороже. В последнее время для улучшения геометрии блоков начинают применять фрезерование поверхностей.
— 3. Необходимость защиты от прямого воздействия влаги.
Ничем не защищенная кладка в теории может быть проницаемой для больших напоров ветра, но реального подтверждения такого явления не получено. Нанесение на поверхность штукатурных покрытий решает проблемы с проницаемостью.
— 4. Высокая стоимость арболитовых блоков.
Это связано с недостаточными автоматизацией производственных процессов, степенью проработки технологии и скромными объемами производства. В итоге себестоимость пенобетонных и газобетонных блоков ниже в 1,5 раза.
— 5. Наличие ограничений в выборе отделочных материалов.
Для правильной эксплуатации важно сочетать с арболитовой кладкой только «дышащие» варианты отделки.
Достоинства арболитовых блоков
Тех, кто решается на строительство по арболитовой технологии, должны вдохновлять ее многочисленные достоинства:
+ 1. Экологичность материала.
Даже входящие в его состав минерализаторы не выделяют в атмосферу вредных веществ.
+ 2. Высочайшая паропроницаемость.
+ 3. Легкость материала.
Легкость материала и его упругость не требуют устройства мощного и жесткого фундамента. Дополнительным бонусом является сейсмостойкость.
+ 4. Легкость обработки.
+ 5. Простой монтаж крепежа.
В арболит можно вбивать гвозди и вкручивать саморезы, как в дерево.
+ 6. Низкая теплопроводность.
Отличное сопротивление теплопередаче при достаточной для малоэтажного строительства прочности позволяет обходиться без дополнительного утепления и получать однослойную структуру стены.
+ 7. Низкая звукопроницаемость.
+ 8. Отказ от армирования.
Возможность отказаться от армирования кладки и устройства монолитных поясов на небольших объектах.
+ 9. Биологическая стойкость.
+ 10. Негорючесть.
Если вы заметили ошибку, не рабочее видео или ссылку, пожалуйста, выделите фрагмент текста и нажмите Ctrl+Enter.
Общая характеристика арболита
Арболит – строительный материал, являющийся разновидностью легкого бетона, в нашей стране еще недостаточно широко распространен. В то время как за границей он существует под названиями дюризол и велокс и служит теплоизоляционным и конструктивно — теплоизоляционным материалом.
Основу арболита составляет древесный заполнитель и цемент. Его не следует путать с опилкобетоном, потому что щепа для него изготавливается специально и имеет свою фракцию и геометрию. Эти особенности утверждены ГОСТОМ 19222-84 «Арболит и изделия из него». Изделия из этого материала производят в виде блоков, плит, панелей.
Изделия из арболита классифицируют, в зависимости от назначения:
- для теплоизоляции и конструктивной теплоизоляции;
- армирования – армированные и неармированные;
- наружного профиля – гладкие и из сложного профиля;
- отделки поверхности — фактурные и нефактурные.
Арболит разделяется в зависимости от марок: 5; 10; 15; 25; 35; 50. Марки означают прочность арболитовых блоков, в зависимости от их предназначения. Теплоизоляционный имеет плотность до 500 кг/м3, конструкционный — плотность свыше 500 до 850 кг/м3. К теплоизоляционному относится арболит М 5,М 10, М15; к конструктивному М 25, М 35, М50.
Арболит используется при возведении жилых, гражданских, производственных зданий не более двух этажей, в качестве наружных несущих конструкций и внутренних стен помещений, теплоизоляции.
Преимущества и недостатки арболита
- высокий уровень тепло и звукоизоляции;
- высокая пожароустойчивость;
- устойчив к гниению;
- экономичен и недорог в строительстве;
- достаточно прочен, при нагрузке не ломается, а только продавливается. экологически чистый материал;
- в нем надежно крепятся гвозди, шурупы без дополнительного применения деревянных основ.
Однако, арболитовые конструкции без применения пароизоляции допущены к эксплуатации только в условиях сухого и нормального влажностного режима. При относительной влажности воздуха внутри помещения более 60% стены из него должны быть защищены пароизоляционным материалом.
Арболит не применяют для строительства цокольных этажей, карнизов, стен подвалов. Арболит следует защищать от атмосферных осадков путем гидрофобной окраски.
Состав арболита
Арболит изготавливается из древесного заполнителя, минерализатора, химических добавок и воды.
Органические составляющие
В качестве древесного наполнителя используют отходы древесины (сосна, ель, пихта, береза, осина, тополь) камыш, костру конопли, льна. Наиболее используемым древесным составом является деревянная щепа или дробленка и древесная стружка в соотношении 1:1 или 1:2. Вместо опилок можно использовать конопляные стебли или костру льна. Костру льна, из-за содержания в ней сахаров, разрушающих цемент, необходимо предварительно погрузить в известковое молоко (расход 50 кг извести на 200 кг костры) и выдержать 1-2 дня в куче. Другим способом является — выдерживание костры конопли, льна на открытом воздухе в течение 3-4 месяцев, тогда арболитовые блоки будут соответствовать показателям прочности. Форма костры имеет важное значение — она должна быть игольчатой длиной от 15 до 25 мм, шириной в 2-5 мм.
Минеральные вяжущие составляющие
Минерализатором в составе арболита выступает портландцемент 400, 500 или более высоких марок. Его расход зависит от его марки заполнителя арболита.
Обычно расход цемента рассчитывают следующим образом: для приготовления 1м3 арболита марки 15, необходимо умножить его значение на на коэффициент 17, например, 15 х 17 = 255 кг.
Химические составляющие арболита
Технические и строительные свойства арболита определяются химическими добавками. Их применение обязательно вне зависимости от климатических условий, в которых будет сооружаться здание из арболита. Именно химические вещества позволят использовать любой древесный наполнитель без предварительной обработки и выдержки, благодаря их способности нейтрализовать сахара.
В производстве арболита используют следующие химические добавки: хлористый кальций, гашеная известь, сернокислый алюминий, растворимое стекло. Наиболее эффективными являются хлористый кальций и алюминий. Сернокислый алюминий в соединении с сахарами нейтрализует их, обеспечивая возрастание прочности арболита.
Общее количество химических добавок в 1 м3 арболита составляет 2-4 % от общего веса цемента (около 6-12 кг). Добавки применяют как отдельно, так и смешивая алюминий с хлористым кальцием в пропорции 1:1, либо соединяя гашеную известь и растворимое стекло (1:1). Перед соединением с арболитовой смесью эти добавки необходимо растворить в воде.
Необходимые пропорции добавок зависят от вида арболита. Для арболитовых блоков марки 30 соотношение добавок следующее: сернокислый алюминий и хлористый кальций (1:1) в пропорции 4% от веса цемента; сернокислый натрий и хлористый кальций (1:1) в объеме 4% от веса цемента; сернокислый натрий и хлористый алюминий (1:1) в пропорции 2% от веса цемента; хлористый алюминий и хлористый кальций (1:1) в пропорции 4% от веса цемента.
Для арболитовой смеси марки 35 хлористый кальций добавляют в пропорции 2% от всей массы цемента. Использование хлористого кальция повышает прочность арболита. Для этого применяется жидкое стекло — силикат натрия или кальция, растворенные в горячей воде в количестве 8—10 кг на 1 м3 арболита.
Технология изготовления арболита
Производственная схема содержит следующие стадии:
- Дробление и придание необходимой формы заполнителю.
- Предварительная обработка органического заполнителя химическими составами.
- Дозирование составляющих компонентов для арболитовой массы.
- Подготовка арболитовой смеси.
- Формирование арболитовых блоков.
Дробление и придание необходимой формы заполнителю.
Перед дроблением куски и отходы древесины складываются в кучи и выдерживаются под навесом около месяца при положительной температуре. Затем эти отходы необходимо превратить в щепу на специальных машинах.
Отходы от деревопереработки, лесопиления подаются на приемную площадку, там они складируются, потом направляются в принимающую воронку рубильного механизма (ДУ-2). Для измельчения древесины рекомендуют пользоваться барабанной рубительной машиной, имеющей широкий спектр применения. Она может обработать практически каждый тип древесных отходов — рейки, кругляки, горбыль, обрезки, отторцовку, кривоствольную древесину. Обработанная таким образом щепа направляется в бункер, а затем идет в молотковую дробильную машину (ДМ-1), после этого древесная дробленка отправляется на вибрационный грохот, в целях отсеивания отходов и слишком крупных частиц.
На выходе дробленка представляет собой фракции древесины игольчатого или пластинчатого вида длиной от 2 до 20 мм, шириной от 2 до 5 мм, толщиной не больше 5 мм.
Предварительная обработка органического заполнителя химическими составами
Измельченная щепа с необходимым гранулометрическим составом направляется через промежуточный бункер в бак с водой для вымачивания и удаления, вредных для производства сахаров и веществ. Туда же направляют хлорид кальция. Вымачивание щепы при гидромодуле 1:10 продолжается 6 часов при температурном режиме 20°С. Применение предварительной гидротермической обработки улучшает физико-механические качества арболита. В воде древесина разбухает и этот процесс происходит до насыщения влагой волокна на 30%, при этом объем древесины и отдельные ее составляющие увеличиваются.
Дозирование составляющих компонентов для арболитовой массы
Важным условием однородности состава арболитовой массы и ее высокой стабильности является точное дозирование и качественное смешивание всех компонентов. Древесную щепу дозируют с помощью объемно — весового способа, с учетом коррекции насыпной плотности материала. Дробленке перед подачей на дозирование нужно иметь положительную температуру.
Для дозирования воды и химических добавок (хлорида кальция) используют автоматические дозаторы турбинного типа, работающие в цикличном либо непрерывном режиме. Возможен вариант дозирования добавок с помощью весового дозатора воды. При расчете дозировки воды и химических наполнителей учитывается влажность органического заполнителя и, соответственно, корректируются объемы добавляемой жидкости. Расчет доз цемента производится с помощью автоматических весовых дозаторов.
Загрузка и дозирование составляющих арболитовой смеси должна идти в следующей последовательности:
1) Древесный органический заполнитель.
2) Цемент.
3) Вода или водный раствор химических компонентов, регулируемый через расходомер.
4) Химические добавки, поступающие в течение всего процесса.
Подготовка арболитовой смеси
После вымачивания, дробленные деревянные фракции направляют в циклический смесительный механизм, являющийся бетономешалкой с принудительным действием. В смеситель подают из дозаторов вяжущие компоненты, воду, химические добавки. Там происходит смешивание всех составляющих до однородного состояния. Во время смешения вводят хлорид кальция с помощью метода дождевания и дозирования из перфорированных труб-распылителей. Данный способ точно вводит хлорид кальция и равномерно распределяет его, улучшая технологические свойства арболита. Все составляющие примешиваются в течение 10 минут. После смешивания из массы можно формировать арболитовые блоки.
Формирование арболитовых блоков
Приготовленная арболитовая смесь направляется через специальные бункеры-укладчики в металлические формы или разборные деревянные формы, там смесь утрамбовывается и уплотняется, с помощью пресса, силового вибропроката и виброштампования. Чтобы арболит, произведенный на стандартном портландцементе , достиг 50% прочности от марки, его выдерживают в формах 5 суток при температуре 15° С и относительной влажностью воздуха около 60-70%.
Можно также залить арболитовую массу в формы и выдержать ее в течение 24 часов при температуре 40° С и аналогичной влажностью. В таких условиях блоки выдерживаются 2 суток с сохранением постоянной температуры не ниже 15° С.
Далее происходит распалубка смеси на блоки, панели и изделия поступают на склад.
Наряду с описанной выше технологией, существует вариант приготовления арболитовых блоков, с древесным заполнителем из одубины — щепы древесины дуба, являющейся отходом производства экстрактов дуба.
Процесс производства арболита из одубины более прост, так как данный заполнитель не нуждается в дополнительном измельчении. Также существует технология изготовления арболита из высокопрочного гипса, которая гораздо проще, чем на базе цемента. Это происходит из-за того что гипс, взаимодействуя с водой, образует нейтральную среду, а не щелочную, которая вызывает выделение сахара из дерева. Так как нет факторов, снижающих отвердение цемента, то использование минерализующих добавок в производстве не требуется. Технология упрощается еще и в связи с тем, что используя высокопрочный гипс, можно применять дробленку гораздо крупнее по фракции, прошедшую только одно измельчение в рубильном механизме.
Таким образом, производство арболита на основе гипса менее затратное, чем при использовании цемента.
Щепа для арболита своими руками Арболит: недостатки и достоинства строительного материала Достоинства и недостатки кремнегранитных блоков
Для малоэтажного строительства создано множество разновидностей материалов. Одни из них используются чаще, другие – реже.
Несмотря на то, что арболит не является новинкой на строительном рынке, многие потребители не знают ничего о его технологии производства, об особенностях, преимуществах и недостатках.
Что это такое?
Арболит – облегченный бетонный материал, изготовленный с применением органических наполнителей. Он легче большинства конструкционных стройматериалов. Например, он обладает более низкой массой по сравнению с классическим кирпичом или искусственным камнем.
Технология производства арболитовых блоков во многом определяет их технические характеристики и эксплуатационные качества. Материал должен выпускаться в строгом соответствии с нормативами ГОСТ.
Однако некоторые производители используют некачественное сырье, в результате чего получают блоки, не отвечающие заявленным характеристикам.
Состав
В арболитовую смесь могут входить различные составляющие. Согласно ГОСТ 19222-84 арболит должен состоять из нескольких компонентов.
Органический наполнитель – щепа. Чтобы получить качественные блоки, должны использоваться древесные частицы с размерами, не превышающими 30, 10 и 5 мм в длину, ширину и толщину соответственно. Помимо этого, в древесине содержание полисахаридов не должно превышать 2%. В органическом наполнителе не должно быть пораженных грибком элементов или различных механических включений. В зависимости от вида арболита содержание щепы колеблется в пределах от 75 до 90%.
Цементное вяжущее. В качестве такого заполнителя должен использоваться портландцемент, имеющий марку не ниже М400. Некоторые производители предлагают блоки, изготовленные на основе морозостойкого цемента. Следует учесть, что при длительном хранении цементные блоки теряют первоначальные характеристики, из-за чего они могут не соответствовать требованиям, заявленным производителем.
Чтобы не столкнуться с такой проблемой, опытные строители рекомендуют покупать арболит из цемента не ниже марки М500.
Компоненты химического происхождения. Арболитовые блоки частично состоят из органических заполнителей, которые имеют свойство гнить. Чтобы избежать поражения щепы грибком, в смесь добавляются различные химические добавки. Это могут быть хлориды кальция или аммония, сульфат алюминия или другие неорганические вещества. Такие компоненты отличаются безвредностью для здоровья человека. Они позволяют не только защитить древесную щепу от преждевременной порчи, но и ускорить процесс адгезии компонентов арболитовой смеси, при этом сократив время высыхания блоков.
Для создания арболита также используется вода. Ее качество регламентируется ГОСТом 23732-79. В воде не должны содержаться жиры и производные липидов, красящие компоненты. Для производства блоков применяется только пресная жидкость.
Перед тем как приступить к технологическому процессу, вода и химические составляющие подвергаются лабораторным исследованиям. Их проводят регулярно для каждой вновь поступившей партии.
Разновидности
Производители выпускают несколько видов такого класса бетона. Речь о них пойдет ниже.
- Строительные блоки. В эту группу входит теплоизоляционный и конструкционный материал. Эти составляющие применяются в различных сферах. Первый обладает небольшой плотностью, благодаря чему он используется для укладки теплоизоляционной основы при возведении межкомнатных перекрытий. Конструкционный вариант имеет плотность, примерно равную 800 кг/куб. м (из-за большего содержания цемента). За счет более высокой прочности такой арболит применяется для сооружения несущих стен и опорных конструкций.
- Арболитовые плиты. Применяются в качестве теплоизоляционного материала. Их плотность не превышает 500 кг/куб. м.
- Блоки с декоративной облицовкой. Такие изделия могут быть отделаны мраморной крошкой или облицовочной плиткой. Эти материалы стоят гораздо дороже обычных блоков. Однако строение, при помощи которых оно возведено, не нуждается в дальнейших работах по декоративной отделке фасадной части.
- Раствор. Он готовится непосредственно на стройплощадке и не подлежит хранению. Раствор применяется для создания монолитных изделий. Чаще всего он используется для утепления жилых помещений, гораздо реже – для возведения небольших сооружений. Помимо этого, из него изготавливается несъемная опалубка для сооружений, чья высота не превышает 3 этажей.
- Гипсовый арболит. Его отличие от обычного – использование при производстве гипса, вместо портландцемента. Он обладает существенными преимуществами: не требует применения химических составляющих и быстро отвердевает.
Как и любые сертифицированные строительные материалы, блочный арболит выпускается в определенных размерах. Самыми «ходовыми» считаются изделия в форме параллелепипеда с параметрами длины, ширины и высоты, равными 500, 300 и 200 мм соответственно.
Технология изготовления
Производство арболита в блоках на крупных предприятиях автоматизировано. Процесс изготовления включает несколько этапов, которые описаны ниже.
- Загрузка органического наполнителя в дозатор. Дозирующее устройство фиксируется на подъемнике, который доставляет компонент в емкость смесительного оборудования.
- Загрузка химических реагентов.
- Добавление портландцемента определенной марки.
- Тщательное перемешивание составляющих смеси до получения однородной массы. Полученный раствор направляется на вибрационный стол с вибропрессовочным устройством.
- Разравнивание массы в формах. На этом этапе происходит сжимание изделий за счет применения пресса. При необходимости получения блоков нестандартных форм в ячейки вручную вставляются специальные пластины. В результате получаются треугольные или трапециевидные изделия.
- Отправка блоков в сушильные камеры. Температура, при которой изделия должны подвергаться сушке, не регламентирована ГОСТом. Однако материалы допускается оставлять в камере не более чем на 24 часа.
Изготовить арболитовые блоки можно и в домашних условиях. Самостоятельное создание материала – сложный процесс. Он потребует тщательной подготовки всех компонентов.
Особое внимание здесь нужно уделить древесной щепе. Из всех пород древесины предпочтительнее будут хвойные породы, такие как пихта или сосна. Присутствие коры или хвои не должно быть более 5% по отношению к общей массе.
При создании блоков в домашних условиях не у каждого строителя под рукой могут оказаться химические добавки. Без них процесс адгезии будет значительно затруднен, а также увеличится время затвердевания изделий (порой на высыхание уходит несколько недель). Самостоятельное изготовление материала высокого качества своими руками маловероятно. Чаще всего в домашних условиях создают блочные изделия для строительства сооружений с низкими эксплуатационными требованиями.
Сфера использования
Арболитовые блоки – строительный материал, который активно применяется в частном строительстве. Из него сооружают дома и коттеджи, различные постройки хозяйственного назначения. Блочные изделия отлично сохраняют тепло, из-за чего их допустимо применять даже в суровых климатических условиях. Помимо этого, материал является довольно прочным, за счет чего он пользуется популярностью в сейсмически активных областях.
В малоэтажном строительстве арболит используется как для возведения построек «с нуля», так и для утепления стеновых конструкций и напольной поверхности. Арболитовые блоки нашли свое применение при сооружении помещений складского, производственного и сельскохозяйственного назначения. Из него получаются теплые гаражи, бани, сараи и различные подсобные строения.
Преимущества
Чтобы решить, стоит ли выбирать арболит в качестве основного строительного материала, следует заранее изучить его свойства, а также плюсы и минусы. Ниже рассмотрены достоинства блочных изделий.
- Экологическая чистота. При производстве материала не используются химические компоненты, которые выделяют вредные для здоровья человека вещества при строительстве или последующей эксплуатации сооружения.
- Высокие показатели прочности на изгиб. При осадке почвы или сезонных движениях грунта большинство стройматериалов трескается, что приводит к образованию трещин внутреннего декоративного покрытия. Арболитовые блоки – иные изделия. Они способны деформироваться, не допуская растрескивания.
- Небольшая масса. Вес 1 куб. м арболита составляет не более 700 кг. Такой же объем кирпича имеет массу 2 тыс. кг. Строителям малый вес материала позволяет отказаться от сооружения массивной фундаментной основы, что экономит время, силы и средства.
- Быстрая кладка. При строительстве сооружений чаще всего отдается предпочтение крупногабаритным блокам (500×300×200 мм). Благодаря большим размерам материала можно создать теплоемкое сооружение за короткий временной отрезок.
- Малый расход песчано-цементной смеси.
- Отличные теплоизоляционные свойства. Арболитовые блоки обладают низкой теплопроводностью, за счет чего они не пропускают холод извне и не отдают тепло, накопленное в помещении.
- Пожаробезопасность. Арболит – практически негорючий материал. Входящие в состав арболитовой смеси химические добавки способствуют повышению огнеупорности блоков до 3 часов. При воздействии пламени огня изделия не выделяют едкого дыма.
- Хорошая паропроницаемость. Арболитовая кладка способна «дышать». Она способствует естественной циркуляции воздуха, что обеспечивает хороший микроклимат в любом помещении.
- Биологическая устойчивость. Возведя сооружение из арболита, можно не бояться, что его перекрытие или стены будут поражены плесенью или другими видами грибка. Это позволяет сохранить деньги на покупку антисептических средств.
- Механическая стойкость. Блоки арболита довольно прочны. Им не страшны удары, падения и другие механические воздействия. Такая устойчивость доказана экспериментально: изделия с трудом разбиваются кувалдой и сохраняют свою целостность при падении с высоты до 18 метров.
- Отличное поглощение шумов. Звукоизоляция материала лучше показателей шумопоглощения древесины или кирпича.
- Возможность обработки. При необходимости блоки можно пилить обычной бензопилой, получая нужный размер изделия.
- Простой монтаж крепежных элементов. В арболитовые блоки без особых усилий вкручиваются саморезы или вбиваются гвозди.
Несмотря на многочисленные преимущества, арболит выбирает не каждый строитель. Причина проста – это недостатки материала. Для одних они являются несущественными, в то время как для других – серьезное основание для отказа от покупки арболитовых блоков.
Недостатки
Арболит имеет много преимуществ, чуть меньше – минусов. К главному недостатку относят высокие риски приобретения модулей кустарного производства. Дело в том, что качественные блоки выпускают на крупных производственных предприятиях, которых не найти в регионе.
В мелких городах и некоторых мегаполисах работают «кустарники» или компании-однодневки. С целью уменьшить себестоимость готовой продукции, они нередко используют дешевое некачественное сырье.
Такие производители не задумываются об эксплуатационных качествах выпускаемых стройматериалов. Они изготавливают модули, нарушая технологический процесс. В результате они реализуют арболит, технические характеристики которого существенно ниже заявленных.
К еще одному минусу относят малую плотность материала. С одной стороны, это положительный момент, поскольку снижается нагрузка на фундамент, а с другой – такие блоки нельзя использовать для возведения многоэтажных сооружений.
Существует ряд других недостатков такого материала.
- Отклонения в размерах. Готовые блоки могут существенно различаться по типоразмерам, прописанным регламентом. Иногда из-за несоответствия параметров строителям приходится увеличивать толщину швов. Это ведет к образованию «мостиков холода» и промерзанию швов в стужи.
- Биологическая неустойчивость. Блоки из арболита – изделия, которые «полюбились» грызунам. Мыши и крысы делают в них многочисленные норки и ходы, что значительно снижает срок службы постройки. Чтобы защитить конструкцию от таких вредителей, потребуется делать бетонный цокольный этаж. А это дополнительные денежные растраты на стройматериалы и наем строительной бригады.
- Необходимость в декоративной отделке фасада. Арболит – эстетически непривлекательный строительный материал (если речь не идет об изделиях с облицовкой). Чтобы улучшить внешний вид строения, не обойтись без финишной отделки. Она повлечет за собой расходы на покупку облицовки и наем рабочей силы.
- Слабая устойчивость к повышенной влажности. Арболитовые блоки способны накапливать влагу, что со временем разрушает материал. Чтобы строение из арболита прослужило как можно дольше, нужно сделать фундаментную основу с хорошей гидроизоляционной оболочкой и произвести оштукатуривание внешней части стены.
- Высокая стоимость. Здесь не идет речь о блоках низкого качества кустарного производства. Изделия, соответствующие нормативам ГОСТ, стоят недешево. Их цена примерно в 1,5 раза выше по сравнению со стоимостью газобетона или пеноблока.
Некоторые недостатки арболита связаны с нарушением технологии его производства или с использованием некачественных составляющих. Чтобы не приобрести блоки, непригодные для строительства, нужно прислушаться к некоторым рекомендациям.
Критерии качественной продукции
Выбор арболита – ответственный процесс, поскольку от него во многом будет зависеть срок службы будущего строения, а также микроклимат внутри него. Опытные строители при покупке материала советуют, в первую очередь, обращать внимание на его стоимость. Маловероятно, что производитель будет работать себе в ущерб и продавать качественные арболитовые блоки ниже их рыночной цены.
Чтобы обезопасить себя от подделки, нужно просить у продавца соответствующие документы на товар (сертификаты качества и соответствия).
Выбирая арболит, важно произвести его визуальную оценку. Ниже приведены показатели качества такого материала.
- Однородность состава. Если арболитовая смесь была неоднородной, готовые блоки со временем будут расслаиваться. Согласно регламенту показатель расслоения должен быть менее 10%.
- Правильная геометрическая форма. Ее нарушения наблюдаются при несоблюдении условий хранения готовых изделий или технологии производства.
- Однородный серый цвет. Неравномерный окрас блоков или посторонние включения говорят о низком качестве изделий. Например, присутствующие зеленые или коричневые оттенки – признак недосушивания изделий. Стоит учесть, что материалы могут иметь различные включения (солому, опилки, хвою, древесную кору), но не более 5%.
- Щепа одинакового размера (наличие частичек с размерами, превышающими установленные нормы, недопустимы). Слишком большие древесные фракции неспособны полностью пропитаться химическими реагентами. Из-за этого они плохо смешиваются с бетоном и снижают прочность готового стройматериала.
Нужно отказаться от приобретения блоков, изготовленных на основе опилок, а не щепы. Такие блоки обладают меньшей прочностью, обусловленной плохой армирующей связкой.
Чтобы точно быть уверенным в качестве арболита, следует договориться с производителем о возможности лабораторной проверки выборочных образцов материала из выпущенной партии.
Отзывы
Узнать о том, какие дома получаются из арболита, помогут отзывы их владельцев. В сети встречаются как положительные, так и отрицательные отклики.
Среди преимуществ покупатели отметили:
- быстроту и легкость возведения строения;
- отличную звуконепроницаемость;
- сохранение тепла зимой и осенью.
Потребители также отметили возможность сохранить деньги на аренде спецтехники при постройке дома, поскольку блоки перемещаются вручную по причине легкого веса.
Судя по откликам, положительно отзываются об арболите лишь те покупатели, которые приобретали материал у крупных и известных производителей. Однако в сети встречаются и отрицательные мнения. Их в большинстве оставляют люди, производящие арболитовые блоки собственноручно. Они отметили следующие негативные факторы:
- сырость и холод внутри помещения;
- неприятный запах, который не выветривается;
- промерзание межблочных швов;
- большой расход штукатурной смеси.
Арболитовые блоки – выбор тех, кто желает быстро и недорого возвести хозяйственную постройку или жилой дом. Чтобы помещение было теплым, сухим и тихим, следует покупать только качественные строительные изделия по реальной рыночной цене.
О плюсах и минусах арболита смотрите в видео ниже.
Арболит является одним из представителей легкого бетона и используется при строительстве зданий и сооружений любого предназначения. Возведение загородных домов, дач и надворных построек станет бюджетным мероприятием, если в качестве основного материала выбрать арболит. Его применяют в виде блоков для устройства наружных несущих стен и внутренних перегородок, а также из него изготавливают различные плиты и панели.
Оглавление:
- Из чего состоит арболит?
- Пропорции компонентов и нюансы изготовления
- Плюсы и минусы
Технические характеристики:
- плотность: 600-650 кг/м3;
- прочность на сжатии: до 1 МПа;
- прочность на изгибе: до 1 МПа;
- теплопроводность: 0,07-0,17 Вт/мхК;
- морозоустойчивость: 50 циклов;
- звукопоглощение: 126-2000 Гц;
- поглощение влаги: 40-85%;
- усадка: 0,5%.
Состав блоков
Арболит производят из древесного наполнителя, связующего, химических составляющих и воды. Древесный заполнитель присутствует в виде отходов деревообработки (ель, пихта, осина, сосна, береза, тополь) и растениеводства (льняная костра, рисовая солома, стебли хлопчатника). Очень крупные частицы после намокания увеличиваются в объеме, это может привести к последующему разрушению, а мелкие возьмут на себя больше цементного раствора. Оптимальный их размер – 40х10х5 мм. Его химическая активность является основным недостатком, поэтому введение древесины свежесрубленных деревьев в состав арболитовых блоков крайне не рекомендуется.
Наиболее востребованным органическим составом считается стружка древесная и щепа в пропорции 1:1 или 1:2. Помимо опилок можно брать отходы льна. Костра должна быть игольчатой формы, шириной 2-5 мм и длиной 15-25 мм. В составе сырья недопустимо присутствие инородных частиц, признаков плесени и гнили, а в зимний период – льда и снега.
Находящийся в льне сахар разрушает цемент, поэтому необходимо ввести в состав арболита химические вещества. Для улучшения качества легкого бетона, костру нужно обработать известковым молочком (2,5 кг извести растворить в 150-200 литров воды на 1 м3 наполнителя) выдержать 2 суток и перемешивать каждый день. Использование этой технологии снизит расход цемента до 100 кг на куб бетона. Еще один способ нейтрализовать сахар – это поместить костру 3-4 месяца на свежем воздухе, что придаст блокам дополнительную прочность.
Минеральным связывающим в составе смеси является портландцемент марки 400, 500 и выше. Чтобы рассчитать количество цемента на 1 куб арболита 16, нужно увеличить его значение в 17 раз. Получается: 16х17= 272 кг. Химические добавки определяют свойства арболитового блока. Независимо от климатического пояса, где будет возводиться сооружение или здание из этого строительного материала, введение их в состав обязательно. Благодаря способности нейтрализации сахара, химические вещества сделают возможным использовать древесные наполнители без ее обработки.
Такими добавками могут служить: растворимое стекло, K2SO4, гашеная известь и CaCl2. Сернокислый алюминий, соединяясь с сахарами, нейтрализует их действие увеличивая при этом прочность готового изделия. Химические вещества применяют как отдельно, так и в сочетании: Al2(SO4)3 и CaCl2 в пропорции 1:1, гашеная известь и растворимое стекло – 1:1. Перед использованием их разводят в воде, после чего соединяют с арболитовой смесью. Общая масса присадок в 1 кубометре не должно превышать 4% от всего веса цемента.
Арболит марки 30 включает добавки: Al2(SO4)3 и CaCl2 – 1:1; Na2SO4 и CaCl2 – в таком же соотношении и в количестве 4 % от всего веса цемента. Na2SO4 и AlCl3 – 1:1 в 2 % от массы связывающей части. При производстве арболита пропорции на 1 м3 замеса должны быть строго соблюдены.
Технология изготовления
Арболитовые блоки можно делать своими руками. Если нужно большое их количество, приобретают бетономешалку, трамбовку, пресс-формы и печь для сушки. Бюджетный вариант предполагает самостоятельное изготовление форм и покупку смесителя составных частей раствора. Пропорции компонентов в арболитовых блоках были рассмотрены выше, поэтому:
1. В бетономешалку постепенно насыпаем древесный наполнитель и заливаем его водой с химическими добавками, тщательно все перемешиваем.
2. Засыпаем портландцемент и, понемногу вливая воду, снова все мешаем.
3. Обрабатываем форму внутри известковым раствором.
4. Готовую смесь накладываем в формы, плотно трамбуя каждый слой. Объем заполняется до уровня 2 см от края.
5. На свободное место укладываем раствор для штукатурки. Разравниваем поверхность при помощи шпателя.
Полученный блок должен находиться в форме около 24 часов, после чего его вынимают и размещают на две недели под навес для постепенной просушки.
Как видно, технология изготовления арболитовых блоков своими руками довольно проста, а соблюдение необходимых пропорций позволит получить на выходе строительный материал, полностью соответствующий его техническим характеристикам.
Преимущества и недостатки блоков
- высокая звуко- и теплоизоляция;
- повышенная пожароустойчивость;
- устойчивость к появлению плесени и к гниению;
- обладает достаточной прочностью;
- отсутствует необходимость в мощном фундаменте;
- легкость и простота монтажа;
- экологичный, невысокая стоимость.
Обладая определенной влагопроницаемостью, конструкции из арболита могут эксплуатироваться в условиях сухого режима. Во всех остальных случаях стены должны быть защищены от влаги изоляционным материалом. При строительстве стен в подвалах и цокольных этажей применение арболитных блоков не рекомендуется. Защитой от воздействия атмосферных осадков служит их гидрофобная окраска или оштукатуривание стен с двух сторон.
Прежде чем самому приступить к изготовлению арболитовых блоков, необходимо все правильно рассчитать и обдумать. При точном соблюдении технологии производства дома из этого строительного материала получатся комфортными, теплыми и недорогими.
Бетон можно использовать различными способами, чтобы воссоздать внешний вид дерева. Некоторые подрядчики используют штампы, другие используют надрезы и окрашивание, а третьи позволяют натуральному зерну настоящих древесных плит оставлять отпечаток на поверхности бетона. Сравните эти методы и получите идеи для своего собственного проекта ниже.
Просмотрите фотографии конкретных проектов, которые копируют дерево.
Брус деревянный Штамповка
идеально подходит для создания новых или наружных патио, которые больше напоминают деревянные палубы.В сочетании с тщательно подобранными цветами, вы можете получить вид, который во многом похож на настоящий, но с повышенной долговечностью и более простым обслуживанием.
Посмотрите на эти популярные модели деревянных штампов и их внешний вид:
Классик Вуд
Множественные деревянные зерна предлагают смелую структуру с досками шириной шесть дюймов.Сидар Вуд Настил
Доски из кедрового дерева шириной три дюйма проложены вплотную.Закаленный Вуд Планка
Доски различной длины с выдержанным внешним видом.Деревянный блок
Деревянные блоки режут перпендикулярно к зерну.Шаблоны любезно предоставлены Brickform,
.Минимальная деревянная и бетонная композицияот Robertson Design
Отказ от ответственности | Эта статья может содержать партнерские ссылки, это означает, что мы можем бесплатно получить небольшую комиссию за соответствующие покупки.
Великолепный дизайн, разработанный архитектором, следует за Robertson Design, прекрасная минимальная композиция из дерева и бетона в идеальном равновесии, в которой уют и тепло дерева плавает над обнаженным необработанным бетоном. Дизайн «Бетонной коробки» нашел свое начало в корнях минималистской японской архитектуры, внутренние пространства остаются открытыми, простыми и честными в своей материальности.
Самыми большими элементами декора являются используемые текстуры и зелень, которая подчеркивает целое.
Бетон из дерева
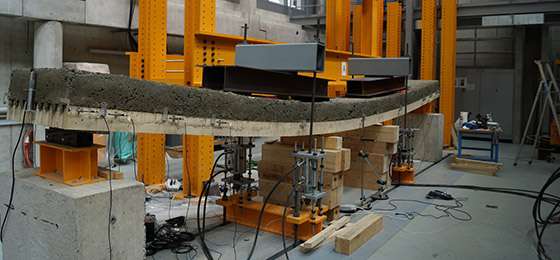
Дома могут быть сделаны из дерева, как это было в прошлом — или из бетона, как они сегодня. Чтобы построить на завтра, два метода строительства объединяются: эти гибридные конструкции, которые содержат как деревянные, так и бетонные элементы, становятся все более популярными в современной архитектуре.
В контексте Национальной ресурсной программы «Ресурс дерева» (NRP 66) швейцарские исследователи в настоящее время разработали еще более радикальный подход к сочетанию дерева и бетона.Они изготавливают несущий бетон, который в основном состоит из дерева. Во многих смесях объемная доля древесины составляет более 50 процентов.
Изделия из цементной древесины существуют уже более ста лет. Еще раньше они использовались только для несущих целей, таких как изоляция. Дайя Цвики, руководитель Института строительных и экологических технологий в Школе инженерии и архитектуры Фрибурга, задалась вопросом, не пора ли более амбициозного использования бетона на основе дерева.
Плавающий бетон
Вместе со своей командой Цвики экспериментировал с содержанием и зернистостью древесины, а также с различными добавками и впоследствии подверг строгим испытаниям различные смеси. Основное отличие от классического бетона состоит в том, что содержание гравия и песка заменяется мелкозернистой древесиной. Другими словами, опилки, а не мелкие камни смешиваются с цементом. Благодаря высокому содержанию древесины новые строительные материалы обладают хорошей огнестойкостью и служат теплоизоляцией.«Они весят не более половины того, что весит обычный бетон — самые легкие из них даже плавают!» говорит Цвики. Более того, поскольку материалы основаны главным образом на возобновляемых ресурсах, после демонтажа они могут быть повторно использованы в качестве источника тепла и электричества. Содержимое древесины может быть сожжено при сжигании отходов, хотя для повседневного использования оно соответствует стандартам противопожарной защиты.
Первоначальные стресс-тесты 1: 1 показывают, что новый древесный бетон также подходит для плит и стеновых элементов и может выполнять несущую функцию в строительстве.Процесс также подходит для сборных единиц. В этом контексте, в частности, группа «Фрибург» хотела бы углубить свой опыт с помощью более широкого спектра испытаний. Исследователи хотят выяснить, какой древесно-бетонный композит лучше всего подходит для каких областей применения и как его можно эффективно производить.
«Пройдет несколько лет, прежде чем мы увидим первые здания, в которых легкий бетон, содержащий древесину, играет важную роль в строительстве», — говорит Цвикки. «Уровень знаний, необходимый для широкого применения, все еще слишком ограничен.»
Инновационные крепления для прочных конструкций
Дополнительная информация: М.Maeder и D. Zwicky: Многофункциональные свойства заливочных древесно-цементных смесей — механические, строительно-физические, экономические и экологические характеристики. Всемирная конференция по лесостроению, Вена, Австрия (август 2016 г.). www.researchgate.net/profile/D… unctional-features-o
М. Эймард и Д. Цвики: Элементы плиты из древесины и древесно-цементных смесей — конструкционные и другие характеристики. 3-я Международная конференция по конструкциям и архитектуре, Гимарайнш (июль 2016 г.). www.researchgate.net / profile / D… Cement-Compounds-Str
Д. Цвики и Н. Макки: Элементы стен из дерева и древесно-цементных смесей — строительно-физические свойства и конструктивные характеристики. 3-я Международная конференция по конструкциям и архитектуре, Гимарайнш (июль 2016 г.). www.researchgate.net/profile/D… -Timber-and-Wood-Cem
Предоставлено Швейцарский национальный научный фондЦитирование : Бетон из дерева (2017, 5 июля) восстановлено 16 июля 2020 г. с https: // физ.орг / Новости / 2017-07-бетон-wood.html
Этот документ защищен авторским правом. Кроме честных сделок с целью частного изучения или исследования, нет Часть может быть воспроизведена без письменного разрешения. Содержание предоставлено исключительно в информационных целях.
,Бетон , в строительстве, конструкционный материал, состоящий из твердого химически инертного вещества в виде частиц, известного как заполнитель (обычно песок и гравий), который связан цементом и водой.
бетон Строительные рабочие заливки бетона. © Дмитрий Калиновский / Shutterstock.comПодробнее на эту тему
строительство: ранние бетонные конструкции
Одним из самых ранних сохранившихся примеров этой конкретной конструкции является Храм Сибиллы (или Храм Весты) в Тиволи, построенный во время…
Среди древних ассирийцев и вавилонян связующим веществом, наиболее часто используемым, была глина. Египтяне разработали вещество, более похожее на современный бетон, используя известь и гипс в качестве связующего вещества. Известь (оксид кальция), полученная из известняка, мела или (где это возможно) раковин устриц, до начала 1800-х годов оставалась основным пуццолановым или образующим цемент агентом. В 1824 году английский изобретатель Джозеф Аспдин сжег и размолол смесь известняка и глины.Эта смесь, называемая портландцементом, остается доминирующим цементирующим агентом, используемым в производстве бетона.
Агрегаты обычно обозначаются как мелкие (размером от 0,025 до 6,5 мм [от 0,001 до 0,25 дюйма]) или грубые (от 6,5 до 38 мм [от 0,25 до 1,5 дюйма] или больше). Все заполнители должны быть чистыми и без примесей мягких частиц или растительных веществ, потому что даже небольшие количества органических соединений почвы приводят к химическим реакциям, которые серьезно влияют на прочность бетона.
Бетон характеризуется типом заполнителя или используемого цемента, специфическими качествами, которые он проявляет, или методами, используемыми для его производства. В обычном строительном бетоне характер бетона во многом определяется водоцементным соотношением. Чем ниже содержание воды при прочих равных условиях, тем прочнее бетон. В смеси должно быть достаточно воды, чтобы каждая частица заполнителя была полностью окружена цементной пастой, чтобы пространства между заполнителями были заполнены и чтобы бетон был достаточно жидким, чтобы его можно было заливать и эффективно распределять.Другим фактором долговечности является количество цемента по отношению к заполнителю (выражается в виде трехкомпонентного отношения — цемента к мелкому заполнителю и крупному заполнителю). Там, где требуется особо прочный бетон, будет относительно меньше заполнителя.
Получите эксклюзивный доступ к контенту из нашего первого издания 1768 года с вашей подпиской. Подпишитесь сегодняПрочность бетона измеряется в фунтах на квадратный дюйм или килограммах на квадратный сантиметр силы, необходимой для разрушения образца определенного возраста или твердости.На прочность бетона влияют факторы окружающей среды, особенно температура и влажность. Если ему позволено преждевременно высохнуть, он может испытывать неравные растягивающие напряжения, которые в несовершенно затвердевшем состоянии не могут быть выдержаны. В процессе, известном как отверждение, бетон остается сырым в течение некоторого времени после заливки, чтобы замедлить усадку, возникающую при его затвердевании. Низкие температуры также отрицательно влияют на его прочность. Чтобы компенсировать это, добавку, такую как хлорид кальция, смешивают с цементом.Это ускоряет процесс схватывания, который в свою очередь генерирует тепло, достаточное для противодействия умеренно низким температурам. Крупные бетонные формы, которые не могут быть надлежащим образом покрыты, не заливаются при низких температурах.
бетон Рабочие, использующие шпатели для выравнивания свежего бетона. Помощник фотографа 2-го класса Эрик Пауэлл / США. Военно-морской флотБетон, который был укреплен на погруженный металл (обычно сталь), называют железобетоном или железобетоном. Его изобретение обычно приписывают Джозефу Монье, парижскому садовнику, который делал садовые горшки и кадки из бетона, армированного железной сеткой; он получил патент в 1867 году.Армирующая сталь, которая может иметь форму стержней, прутков или сеток, обеспечивает прочность на разрыв. Обычный бетон не может легко противостоять нагрузкам, таким как воздействие ветра, землетрясения, вибрации и другие изгибающие силы, и поэтому не подходит во многих конструкциях. В железобетоне прочность на растяжение стали и прочность на сжатие бетона делают деталь способной выдерживать любые нагрузки в течение значительных промежутков времени. Текучесть бетонной смеси позволяет расположить сталь в точке, где ожидается наибольшее напряжение, или вблизи нее.
Еще одним новшеством в каменном строительстве является использование предварительно напряженного бетона. Это достигается с помощью процессов предварительного или постнапряжения. При предварительном натяжении отрезки стальной проволоки, кабелей или канатов укладываются в пустую форму, а затем растягиваются и закрепляются. После того, как бетон был залит и оставлен для схватывания, якоря освобождаются и, когда сталь стремится вернуться к своей первоначальной длине, она сжимает бетон. В процессе постнапряжения сталь пропускается через каналы, образованные в бетоне.Когда бетон затвердеет, сталь прикрепляется к внешней части элемента с помощью какого-либо захватного устройства. Применяя измеренную величину растягивающей силы к стали, степень сжатия, передаваемую бетону, можно тщательно регулировать. Предварительно напряженный бетон нейтрализует растягивающие силы, которые могут разорвать обычный бетон, сжимая область до точки, в которой не возникает натяжение, пока не будет преодолена прочность сжатого участка. Поскольку он достигает прочности без использования тяжелой стальной арматуры, он был использован для создания более легких, мелких и более элегантных конструкций, таких как мосты и обширные крыши.
В дополнение к его потенциалу для огромной прочности и его первоначальной способности адаптироваться практически к любой форме, бетон является огнестойким и стал одним из самых распространенных строительных материалов в мире.