Секреты производства пеллет — ТехноМашСтрой
Сегодня идет речь о полной и глубокой переработке древесины, и особенно актуальным является вопрос по утилизации отходов деревообработки. Мы считаем, что одной из самых наилучших технологий переработки древесных отходов является – производство пеллет. Вот несколько критериев по которым данная технология переработки отходов превосходит другие:
- Технология довольно проста.
- Для обслуживания работы оборудования необходимо минимальное количество персонала.
- Себестоимость производства довольно небольшая, а вот отдача от бизнеса высокая.<
- Возможность переработки отходов различных размеров. Но как мы уже знаем, чтобы эффективно работать, необходимо знать технологию производства продукции от А до Я. И здесь к технологии производства относится:
- Сырье, с его размерами и влажностью.
- Процесс работы оборудования и режимы работы.
- Качество получаемых пеллет.
- Правильная упаковка пеллет.
При этом в интернете имеется достаточно большое количество информации про оборудования различных фирм. Но вот как работать на таком оборудовании никто не говорит, какое сырье предпочтительнее, какие нормы расхода сырья, как увеличить ресурс работы линии.
Сырье для производства пеллет
Сырьем для пеллет является измельченная древесина размером около 1 мм толщиной и до 3-4 мм длиной. Преимуществом производства пеллет является тот факт, что здесь не требуется специально подготовленная стружка как к примеру для дсп. В сырье не допускается наличие минеральных примесей и металлических включений. Сырье для производства пеллет оказывает влияние на цвет готовых гранул:
- Черные пеллеты получают из древесины с наличием коры, и возможным наличием гнили несоблюдением технологии…
- Серые пеллеты получают из неокоренной древесины.
На фото видно что пеллеты имеют включения коры. При уменьшении размера стружки включения могут быть и не видны, но пеллет будет иметь темноватый оттенок.
- Светлый пеллет получают из качественной окоренной древесины. Светлый пеллет обладает большей теплоотдачей, меньше крошится и соответственно дороже стоит чем серые и черные гранулы.
Кроме цвета пеллет, от сырья зависит и качество склеивания пеллет. Дело в том что связующим веществом в процессе прессования пеллет является природный лигнин, который содержится в древесине. Но содержание лигнина в каждой породе разное, и соответственно чем больше лигнина содержится в древесине тем качественнее пеллет.
Еще одним важным технологическим фактором при производстве гранул является такой параметр древесины как твердость. Дело в том что чем жестче древесина, тем больший износ режущего инструмента, матрицы и пуансона пресса.
Как влияет сырье на получение пеллет
Сегодня рассмотрим сырье для пеллет получаемых из опилок. Мы знаем что опилки могут быть разными и различаться по породе, по размерам, по влажности… Также мы рассмотрим какие параметры и как влияют на производство пеллет и это особо важно как нам кажется при производстве пеллет своими руками, так как промышленное оборудование не столь чувствительно как небольшой станок с малой мощностью.
Влияние породы древесины на склеиваемость пеллет из опилок
Теперь переходим к основной теме этой статьи. Пеллеты могут производиться из разных пород древесины, я же хочу рассказать из какой древесины пеллеты будут получаться лучше, какая древесина подходит оптимально, в общем рассмотрим некоторые критерии сырья для пеллет…
Сосна–27,05%.
Ель–27,00%.
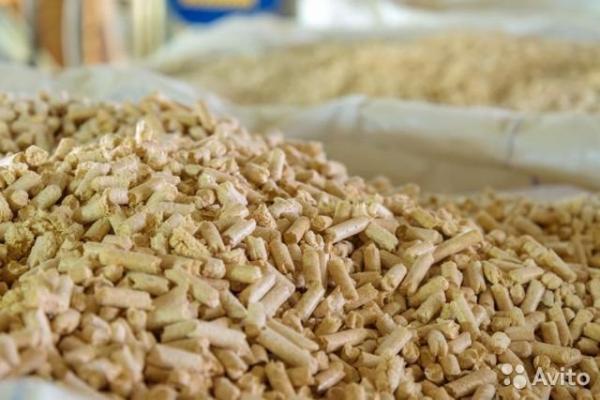
Пихта–29,89%.
Бук–27,72%.
Береза–19,10%.
Осина–21,67%.
В среднем в древесине хвойных пород лигнин содержится в пределах 26-30%, в лиственных породах 19-28 % от общей абсолютно сухой массы древесины. Ну и конечно чем ниже содержание лигнина, тем большее количество отсевов мы получаем, а это большие затраты электроэнергии и незначительные снижения производительности.
Влияние твердости дерева на получение пеллета
Еще одним интересным фактором в производстве пеллет является твердость древесины, чем тверже древесина, тем более сложно ее переработать в стружку, сложнее спрессовать в пеллет. Повышается расход электроэнергии, увеличиваются нагрузки и соответственно расход инструмента (ножи, матрица, ролики). Предлагаю вам сравнить твердость некоторых пород.древесины:
Сосна–260кГ/см2.
Ель–235кГ/см2.
Пихта–255кГ/см2.
Бук–555кГ/см2.
Береза–425кГ/см2.
Осина – 240 кГ/см2.
Опять же один кубометр пеллет из опилок более плотных пород будет обладать большей насыпной плотностью и большей теплотой сгорания. К примеру один кубометр пеллет из березы выделит больше тепла чем один кубометр пеллет из опилок сосны.
Работа линии по производству пеллет
Итак, прессование осуществляется за счет продавливания через матрицу мелких опилок. Опилки просыпаются на матрицу и затем вдавливаются в отверстия роликами катающимися по матрице. износ роликов пуансона и матрицы огромное влияние оказывает очень интересная технология запуска пресса
Пресс пеллет – подготовка к работе В свое время когда я только начал изучать изготовление гранул, я и не думал что это производство именно с таким количеством нюансов, и технология производства пеллет так чувствительно к настройке пресса. Очень часто можно встретить такую ситуацию что пеллет не идет или вообще пресс для пеллет невозможно запустить, иначе говоря он запускается, но матрица сразу забивается. Но сначала про запуск пресса (при условии что матрица уже притерта).
Пресс для изготовления пеллет запускается в следующем порядке:
- Включатся основной двигатель вращения пуансона, стружка не подается
- Подается первичная смесь. Под первичной смесью мы понимаем состав масло и опилки. Дело в том что для более мягкого запуска и остановки пресса, а также для увеличения работы матрицы, подается смесь пеллетов или опилок с маслом. Если остановить пресс пеллет с обычной стружкой без масла (в матрице опилки стандартной влажности без масла), то уплотненная стружка как бы прикипает к стенкам матрицы и потом при запуске необходимо очень большое усилие чтобы продавить эту стружку, при этом данного усилия во многих случаях как правило не хватает и пресс просто забивается, в это время идет повышенная нагрузка и соответственно повышенный износ двигателя и передающих механизмов пресса.
Плюсом такого “усовершенствования” является значительная экономия на масле, минусом может служит более быстрый износ матрицы, так как отработка и еже с ней содержит большое количество металлических примесей.
- Ждем когда пойдет пеллет, при этом пеллет с маслом мы убираем или выкидываем (в зависимости от того будете ли вы использовать повторно данную смесь).
- После того как начал продавливаться пеллет через матрицу, включается минимальная подача стружки в пресс, при этом подача стружки с маслом прекращается. Стружка убирается до тех пор пока не появится только пеллет без масла.
- После появления только чистых пеллет без масла скорость подачи опилок в пресс для изготовления пеллет увеличивается, пресс выводится на проектную мощность.
Почему забивается пресс для изготовления гранул
Если пеллет не идет, вы не смогли продавить матрицу, не стоит крутить и мучить пресс, необходимо останавливать всю систему и пробивать или просверливать отверстия матрицы.
Пресс для производства пеллет очень часто забивается опилками, предлагаю вам рассмотреть основные причины его забивания, когда через матрицу не продавливаются гранулы. Будем считать что все технологические параметры в норме:
- Давление пуансона на матрицу в норме
- Влажность стружки 12-15%
- Фракционный состав в норме
Это случается довольно часто, когда пресс для пеллет работал, работал и вдруг нагрузка на двигатель полезла, двигатель выбивает и весь пресс завален опилками. Оператор все очищает, подготавливает матрицу, запускает пресс и после двух трех часов все повторяется снова, пресс останавливается, оператор очищает, при этом все нормально, замечаний по технологии как бы нет. На самом деле когда начинают разбираться выявляются казалось бы незначительные причины, но именно они так негативно влияют на работу пресса:
- Если один из роликов немного болтается или подклинивает – пресс работать не будет
- Если давление пуансона хотя бы немного не стабильно, то есть случается так что по какой то причине (пропускает клапан) с пуансона уходит давление, в таком случае датчик может и не показывать сразу падение давления, так как в это время сила прижима пуансона уменьшается и на матрицу начинает накатываться слой опилок.
Немаловажную роль в оптимизации производства древесных гранул играет автоматизация и визуализация производственного процесса. Конечно же для контроля процесса в настоящее время просто необходимо каждую смену отслеживать какое количество отсева, после сортировки готового пеллета на сите, уходит в повторную переработку, какой коэффициент получается после работы каждой смены (для этого устанавливаются весы измеряющие массу подаваемой стружки на пресс). Необходимо видеть какие скорости пресса были в процессе смены. Очень полезно следить за временем остановки и запуска линии, количеством простоев за смену, стоит понимать что на производстве пеллет каждый запуск и остановка пресса это критические нагрузки и максимальные износы матрицы и роликов, поэтому их просто необходимо отслеживать и сводить к минимуму. Предлагаю вам ознакомиться с ориентировочными нормами расхода при производстве пеллет. При установке новой матрицы и новых роликов для изготовления высококачественных гранул требуется какое то время для притирки рабочих механизмов, поэтому часто на новых механизмах можно не получить желаемое качество. Также существует искусственный вариант выхода из строя матрицы и роликов – попадание твердых инородных частиц (камней, металла), на рабочих механизмах образуются впадины и прессование на данных участках не происходит. Качественное прессование это когда гранулы выдавливаются из всей поверхности матрицы, а не частями. Выдавливание гранул только из некоторых частей матрицы говорит о том что пресс настроен неправильно, причин может быть множество это и выход из строя матрицы или роликов, колебания матрицы в посадочном месте, выход из строя подшипников на роликах и т.д..
Все качественные показатели гранул между собой взаимосвязаны. И как правило при несоблюдении каких то технологических параметров (влажность, давление, фракционный состав) сразу снижаются все качественные показатели окатышей (так ласково их называют в Европе).
Качество пеллет зависит от:
- Правильно выбранной влажности сырья (окатыши со стружки повышенной влажности будут иметь больший объем чем гранулы со стружки пониженной и средней влажности при одинаковой массе)
- От фракционного состава сырья (чем крупнее стружка тем труднее ее спрессовать, при этом готовый окатыш с крупной стружкой может рассыпаться из за восстановления формы спрессованной стружки)
- От породы сырья (хвойные пеллеты получаются более качественные чем из пород лиственной древесины)
- От износа матрицы и роликов (при износе стружка не прессуется а накатывается на матрицу)
- От правильно настроенных зазоров между роликами и матрицей.
- От диаметра прессуемых пеллет (чем меньше диаметр пеллет тем лучше качество пеллет при одинаковых условиях прессования)
ТЕХНОЛОГИЯ ПЕЛЛЕТ ДУМАЮ ТЕПЕРЬ МНОГИМ СТАЛА БОЛЕЕ ПОНЯТНА.
Мини-завод по производству пеллет как бизнес в гараже
Завод по производству пеллет для домашнего бизнеса не требует больших инвестиций. При этом такой мини-завод способен приносить ощутимую прибыль при малых вложениях. Ведь на пеллетном оборудовании производиться альтернативное топливо. Энергоресурсы всегда пользовались высоким спросом во все времена. Бизнес в отрасли энергоресурсов всегда имеет больше шансов на успех и процветание. Пеллеты сегодня все большую популярность набирают как альтернативное топливо. Его производят благодаря переработке отходов древесины и не только.
Доходный потенциал производства пеллет в домашних условиях
Спрос на пеллеты растет с каждым днем. Оптовая стоимость 1т. пеллетного топлива начинается от 110$. Каждому заводу для производства или переработки нужно закупать сырье. Для производства пеллет в качестве сырья используют опилки из древесины, солому, шелуху из подсолнечника и т.п.
Чтобы пеллетным мини-заводом произвести одну тонну топливных гранул потребуется 7,4 кубометра опилок. Стоимость сырья составляет 5$ за куб (на условиях самовывоза). Получаем валовую прибыль: 110$ — (5$ * 7,4) = 73$ и это с одной только тонны альтернативного топлива. Даже при учете всех расходов (электроэнергия, зарплата, упаковка, транспорт) рентабельность бизнеса остается выше 100%.
Показатель доходности завода по производству пеллет один из самых высоких по сравнению с другими видами бизнесов по переработке отходов. Рынок пеллетов охватывает все больше потребительских сфер. Ведь твердотопливные гранулы уже сегодня активно применяют: для отопления помещений, выработки электроэнергии на электростанциях, а так же начинают применять как альтернативу жидкому топливу для грузовых автомобилей с помощью газогенераторов. Бизнес идея по производству пеллетных гранул – это целая энергетическая промышленность, которую можно реализовать при минимальных инвестициях.
На заводе должны производиться качественные пеллеты
Чтобы запустить заводское производство пеллет, следует изучить технологию. Пеллеты были изобретены еще в середине прошлого века. Придумал их Рудольф Гуннерман. Они искал решение для сокращения расходов на вывозе отходов из своей лесопилки. И решил опилки прессовать прямо на заводе перед вывозом, чтобы в несколько раз уменьшить объем отходов. Но оказалось, что прессованные опилки и стружка горят значительно лучше и эффективнее обычной древесины. Благодаря высоким показателям горючести теплотворность пеллет выше в 2.5 раза. Чем больше углерода в древесном топливе, тем выше его теплотворность.
Дело в том, что обычное необработанное дерево кроме горючего углерода в молекулах целлюлозы содержит еще значительное количество водорода и кислорода. А при измельчении дерева молекулы целлюлозы разрушаются и атомы водорода, кислорода из нее уходят в виде летучих газов. Еще существенным преимуществом пеллетных гранул от дерева является сгораемость материала. Дерево при сгорании теряет 85% массы в виде летучих газов, остальные 15% составляет зола. А при сгорании пеллет золы остается всего 0,75-1,5% (почти в 20 раз меньше) в зависимости от сырья из которого они произведены.
Так же важно отметить, что топливные гранулы в 2 раза меньше содержат влаги в отличие от дерева. В процессе производства под высоким давлением пеллеты прогреваются до 110 градусов Цельсия, что позволяет вдвое сократить содержание влаги.
Кроме того за счет прессования топливные гранулы обладают более высокой плотностью чем дерево. Проверить данный факт очень легко. Дерево, как известно в воде не тонет, плавая на поверхности, а пеллетные гранулы, произведенные из древесных опилок, камнем идут на дно. Это так же объясняет, почему из меньшего объема гранулированного топлива получается значительно больше тепла при сгорании, чем у дерева.
Фактически пеллеты это горючее топливо, которое набирает большую популярность во время энергетического кризиса. Оно обладает своими особенностями такими как: высокая безопасность топлива, низкая стоимость и другие преимущества.
Технология производства пеллет для малого завода
Бизнес по производству пеллет – это завод по переработке отходов. Заниматься переработкой отходов – актуально, выгодно и гуманно. Особенно выгодно если перерабатывать отходы в топливо безопасное для окружающей среды. На заводе можно производить пеллеты из различного вида сырья: древесных опилок, стружки, коры, соломы, шелухи подсолнечника, сухих стеблей кукурузы и т.п. Конечно, пеллетные гранулы могут отличаться по своим характерным свойствам в зависимости от сырья, из которого их производят.
Главный показатель, влияющий на стоимость древесных гранул – процент зольности. Чем выше процентное содержание золы, тем ниже стоимость гранулированной древесины.
Технология производства пеллет проста и понятна. Сырье при необходимости следует измельчить до размера мелких опилок (тирсы) и если нужно предварительно подсушить (рекомендуемая влажность сырья до 20%). После чего опилки подаются в роликовый или шнековый пресс-гранулятор где подобно мясорубки выдавливаются через специальную решетчатую матрицу готовые цилиндрические пеллеты. Каждое дерево в своем составе содержит клеящее вещество «лигнин». Благодаря лигнину из опилок формируются цельные гранулы цилиндрической формы. Опилки в прессе-грануляторе нагреваются и выделяют лигнин, который под воздействием температуры превращается в натуральный природный клей. Древесная смола сама по себе горит долго и ровно.
Заводу нужно поставить прессовочное оборудование
Оборудование для завода по производству пеллет вполне доступно как для малого, так и для домашнего бизнеса. Пресса-грануляторы могут быть роликового или шнекового типа.
Стоимость прессов напрямую зависит от производительности. Например, пресса производительностью в 250 кг/час уже доступны по цене 6200$ с мощностью электродвигателя 15 кВт., для 380В. Хотя существуют и более компромиссные предложения с меньшей производительностью и ценой пресса.
Для производства пеллет из соломы заводу потребуется дополнительное оборудование — измельчитель. Можно использовать ДКУ, который обойдется по цене 1000$ с производительностью 100кг/час для фракций размером 3мм.
Важно отметить, что при постоянной работе пресса-гранулятора , через 2,5-3 месяца потребуется замена деталей узлов высокого давления. В управлении производством правильно контролируйте постоянные расходы средств на решетчатую матрицу, ролики или шнек (в зависимости от типа пресса) – основные рабочие части гранулятора. При производстве пеллетов только из соломы или другого мягкого сырья рабочие детали пресса могут прослужить вдвое больше. А так же производительность будет несколько выше при одних и тех же нагрузках, что благотворно отразится на расходах электроэнергии.
Потребность в пеллетах все больше испытывают альтернативные отопительные системы
У каждого производственного или перерабатывающего завода стоит главный вопрос о сбыте продукции. Отопление помещений пеллетами на специальных котлах – сегодня наиболее популярное применение для данной продукции. Но существуют и другие рынки сбыта. Например, в области наполнителей для туалетов домашних животных. В Европе уже давно используют, а у нас только набирают популярность пеллетные (гранульные) котлы с очень высоким КПД (85-85%).
Данный вид твердотопливных котлов отличается своей повышенной продолжительностью работы без участия человека на протяжении 7 суток и более. Такая возможность достигается благодаря сыпучести гранул, с помощью которой осуществляется заправка котла твердым топливом через программный контроллер управляющим шнеком подачи.
Весь процесс дозаправки котла происходит автоматически. Уровень автоматизации котла позволяет самостоятельно подавать новую порцию гранулированной древесины из бункера для поддержания заданной температуры. Специальный электрический тэн и вентилятор могут взять на себя автоматический розжиг топливных гранул. Так же котлы оборудованы специальной гранульной горелкой, которая позволяет максимально эффективно использовать пеллетное твердое топливо.
Пеллетные котлы не требуют особого обслуживания. Чистка золы осуществляется 1 раз в месяц. Мощность котлов начинается от бытовых потребностей 15-500кВт и может достигать до 2МВт для промышленных целей. Срок службы котлов один из самых высоких – более 20 лет. На картинге изображен гранульный котел австрийской фирмы OkoFen. Описание устройства котла:
- Камера рециркуляционного горения.
- Микропроцессорное управление.
- Самоочищающаяся система.
- Пульт управления регулировки температуры.
- Камера из высококачественной стали.
- Гранульная горелка.
- Дополнительная система очистки.
- Электроподжиг топливных гранул.
- Место для установки горелки с обратной стороны.
- Система пожарной безопасности.
- Бокс для пепла.
- Автоматическая подача гранул.
- Климатконтроль.
- Контроллер давления.
- Воздухозаборник.
Пеллетные котлы являются серьезной альтернативой газовым котлам. Хотя сама гранулированная древесина прекрасно себя зарекомендовали как высокоэффективное топливо в обычных твердотопливных котлах и даже простых печках как лучшая альтернатива дровам. Ниже приведены еще примеры потребления эффективного пеллетного топлива.
Пеллетами можно заправлять автомобили
Cбыт пелет заводского малого производства будет существенно расширен. Уже сегодня ездят автомобили на полетном топливе. Всем известно, что в середине прошлого века грузовые автомобили работали на древесном топливе. Двигатель внутреннего загорания тот же самый что и для традиционного топлива. Фактически в место бензина использовался горючий газ, получаемый из газогенератора путем пиролизации древесины.
Газогенератор – это устройство для преобразования в газообразную форму твердых горючих материалов. Данное физическое явления называется пиролиз – распад тяжелых молекул на легкие под воздействием повышения температуры и недостатка кислорода. На пример обычный автомобиль «Газель» оборудован газогенератором расходует 1кг. древесины на 1км. То есть на 100км необходимо было возить в кузове 100кг древесины. Так использовалось много полезного пространства в кузове автомобиля на объем дров и габаритов газогенераторной установки. Дозаправка газогенератора древами осуществлялась вручную через каждые 50км. Разгон автомобиля необходимо было производить плавно, предоставляя газогенератору время для перехода на повышенный режим мощности.
Благодаря пеллетам все недостатки автомобилей на газогенераторных установках практически устраняются. Их сыпучесть позволила автоматически заправлять газогенератор, так как в общей массе они представляют из себя псевдожидкость. Габариты и масса газогенераторной установки стали значительно меньше. Электронная микропроцессорная система отслеживает ускорение автомобиля и автоматически подключает традиционное топливо в момент резкого изменения нагрузок на двигатель акселератором. Приемистость автомобиля полностью сохраняется. К тому же пеллеты благодаря большей плотности и теплотворности активнее выделяют газ и реже нуждаются в паузах для перехода на другую мощность работы генератора. Тем более на грузовых автомобилях.
Все преимущества гранулированного топлива в отношении к древесине пригодились для использования их как топливо для грузовых автомобилей с газогенераторными установками. Плотность и теплотворность топливных гранул требуют значительно меньше полезного пространства в кузове. Пеллеты в 3 раза снизили расход потребления твердого топлива до 0,3кг на 1км. Даже при краткосрочном использовании бензина в моменты резкого ускорения автомобиля, уже расход меньше в 2 раза в отношении к традиционным видам горючего. Если ездить в экономичном режиме, можно вообще отказаться от использования бензина. Тогда стоимость 1км составит 0,04$. 1кг пеллетов = 0,11$ / 3 (расход на 1км = 0,3кг) = 0,04$/км. Еще важно отметить, что при сгорании газа созданного путем перолиза древесных гранул не выделяются вредные, токсичные вещества. Это экологически-чистый вид топлива.
Пеллеты использую как топливо для электростанций
Рынок потребления пеллет растет с каждым днем. К 2020 году Европейский Союз планирует на 20% снизить количество вредных выбросов в атмосферу. Для этого планируется уже в 2015 году увеличить объемы использования твердого БИО-топлива до 50 %. Основными потребителями станут электростанции на пеллетах. На сегодняшний день это самые дешевые «зеленые электростанции» по сравнению даже солнечными и ветровыми станциями.
Пеллеты обладают высокими энергетическими показателями. Все крупные электростанции Европы переходят на гранулированное древесное топливо. Только начинают появляться в продаже мобильные электростанции на гранулированном топливе. Все больше устанавливается котлов, работающих на древесных гранулах.
С подорожанием нефти и газа будут выпускать все больше газогенераторных установок для грузовых автомобилей и сельхозтехники. Сегодня мы находимся в самом начале развития использования нового вида топлива. Потребности в нем будут расти постоянно. Важно отметить, что у малого или домашнего бизнеса уже сейчас имеется возможность начать производить топливо нового поколения при небольших инвестициях. Уже сейчас нужно быть готовым к активному росту рынка.
Процесс изготовления пеллет (☆10 шагов)
Покупка гранулятора на самом деле является очень небольшой частью производства пеллет из древесины или биомассы.

На первый взгляд изготовление пеллет на грануляторах может показаться очень простым делом: вы загружаете древесину или биомассу в гранулятор, а пеллеты выходят с другого конца. Что ж, реальность не может быть дальше от истины, поскольку качественное прессование пеллет из древесины и биомассы основано на сочетании принципов. К ним относятся надлежащая подготовка материала, надлежащая эксплуатация и техническое обслуживание гранулятора. Тем не менее, даже для среднего домовладельца все еще возможно владеть и эксплуатировать небольшой гранулятор. Как и в любом другом процессе, речь идет о мельнице. Как и в любом другом процессе, нужно просто знать, что и когда нужно делать.
- Изменения размера частиц сырья
Перед прессованием пеллет на грануляторах необходимо измельчить древесину, солому, траву или любую другую форму биомассы.

- Изменения влажности сырья, качества окатышей и производительности
Одной из причин популярности пеллетного топлива является то, что содержание влаги в пеллетах составляет менее 10%. Это позволяет пеллетам очень эффективно гореть и практически не выделять дыма при сгорании. Производство пеллет – это высокотемпературный процесс. Правильное содержание влаги позволяет производить гранулы наилучшего качества, снижает потребление энергии и сокращает время простоя гранулятора.
- Изменения в составе сырья и включение связующих и смазочных материалов
В производстве пеллет каждое сырье ведет себя по-разному, и из одних материалов получить качественные пеллеты легче, чем из других.

- Изменения в скорости подачи сырья на гранулятор
Еще одна регулировка, влияние которой на производство пеллет неизвестно, – это скорость подачи в гранулятор. Корректировка скорости подачи и поддержание постоянной скорости подачи могут быть ключевым фактором, определяющим эффективность работы гранулятора, даже если сырье идеально подготовлено.
- Изменения в кондиционировании сырья и пара
Кондиционирование – это предварительная обработка сырья перед поступлением на гранулятор.

- Изменения рабочих температур гранулятора
Температура является ключевым требованием при производстве пеллет. Если в грануляторах не будет достигнута определенная температура, природный лигнин не расплавится. Некоторые гранулы из биомассы, например, древесные гранулы, невозможно производить без достаточного количества тепла. Однако слишком высокая температура может привести к повреждению гранулятора и отдельных расходных материалов, таких как пресс-форма гранулятора, ролики, подшипники и уплотнения.
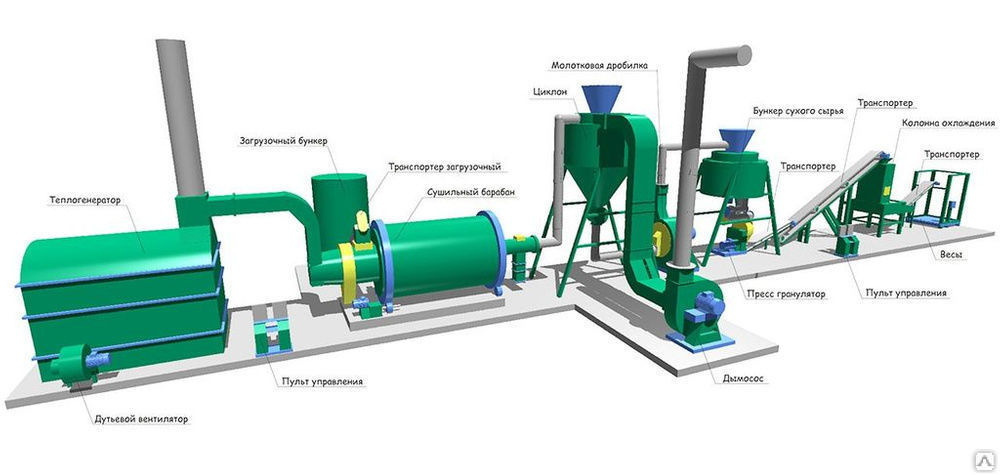
- Изменения зазора ролика и матрицы гранулятора
Другим параметром, который может сильно повлиять на эффективность работы гранулятора, является расстояние между роликом и шаблоном матрицы. Ролик и матрица являются изнашиваемыми расходными деталями из-за абразивной природы и давления сжатия. Расстояние, установленное между роликом и матрицей, может влиять на количество энергии, потребляемой гранулятором, качество гранул, производительность гранулятора и количество производимой мелочи. Правильная установка матрицы на гранулятор также увеличивает срок службы ролика и матрицы и снижает затраты на замену этих расходных материалов.
- Изменения скорости вращения шаблона матрицы гранулятора
Скорости вращения ролика и матрицы влияют на сложные отношения при прессовании гранул. Некоторым материалам требуется большее время сжатия и, следовательно, требуется более низкая скорость вращения.
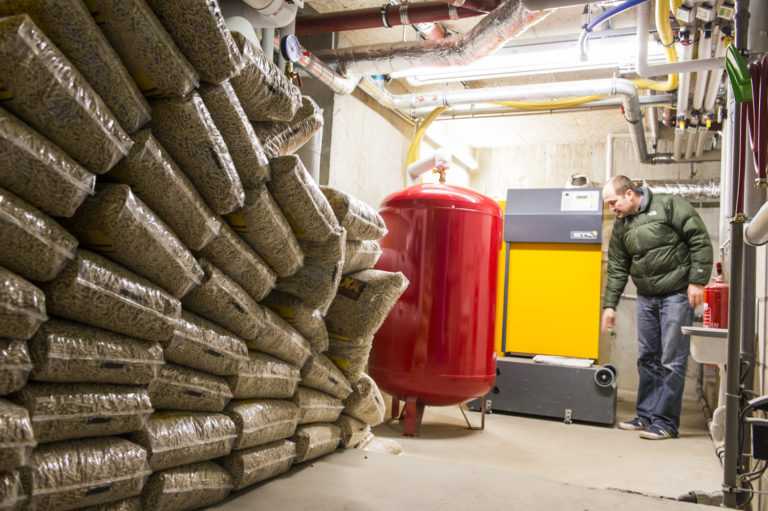
- Изменения в конструкции матрицы гранулятора и используемом металле
Многие различные формы металлических сплавов используются для изготовления шаблонов штампов грануляторов. Различные сплавы металлов имеют определенные преимущества и недостатки. Использование правильного сплава имеет решающее значение для снижения износа и увеличения производительности. Тип используемого металла также влияет на отделку отверстий штампа.
- Полное руководство охватывает 10 этапов производства гранул
Как видно из вышеприведенной информации, изготовление пеллет – это гораздо больше, чем просто добавление материала в гранулятор. По этой причине мы выпустили Руководство по производству пеллет, чтобы помочь потребителям узнать, как производить качественные пеллеты из различных материалов из древесины и биомассы.
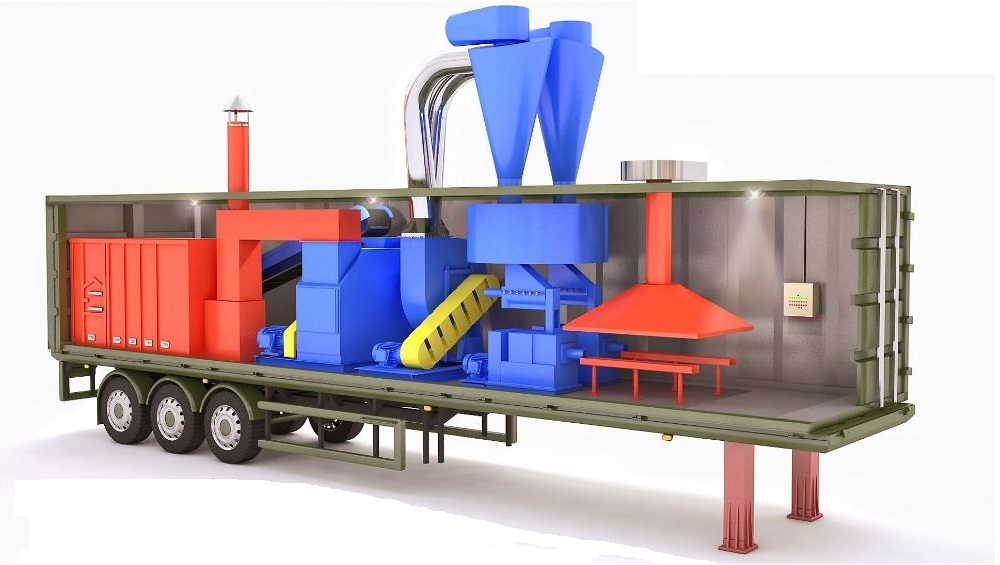
Руководство разбито на десять шагов, как вы можете видеть ниже:
1. Измельчение: Измельчители/Измельчители, Молотковые мельницы
2. Транспортировка материала: Вентиляторы, циклонные сепараторы и шнековые шнеки
33
3. Решения для сушки: вращающиеся/барабанные сушилки, трубчатые сушилки
4. Решения для смешивания: смесители периодического действия
5. Кондиционирование: добавление воды и пара, связующие вещества
6. Производство гранул: грануляторы с кольцевой матрицей
7. Просеивание: Снятие штрафов
8. Охлаждение: противоточные охладители
9. Транспортировка гранул: ковшовые элеваторы
10. Упаковка и хранение: мешки, мешки и бункеры
9 ellet Line, пожалуйста, почувствуйте бесплатно связаться с нами.
У нас есть многолетний опыт работы в этой области,
предложит вам лучшее решение и самую честную помощь.

400-600 кг/ч Линия по производству древесных гранул/Мобильный завод по производству древесных гранул
Перейти к содержимому Мобильная линия по производству пеллет 400-600 кг/ч- Посмотреть увеличенное изображение
Эта полная линия по производству древесных гранул производительностью 400-600 кг/ч имеет комбинированную конструкцию, которая может осуществлять универсальную операцию с управлением электрическим шкафом. Мобильный завод по производству пеллет специально разработан для мелкосерийного производства пеллет, который может удовлетворить ежедневные потребности небольшого завода по производству пеллет или семейного использования. Эту линию по производству древесных гранул также можно назвать передвижной завод по производству древесных гранул 9.0012, так как все необходимое оборудование, такое как дробилка древесины , сушилка опилок , уравнительный бункер , шнековый питатель , гранулятор с плоской матрицей , сито для охлаждения пеллет
3, 1 ковш и 1 электроуправление кабинет размещаются на одной фундаментной раме, экономя много места и снижая затраты на производство пеллет.
В чем основная проблема малого завода по производству пеллет?
Для пользователей, которые хотят вести собственный бизнес по производству пеллет, абсолютно необходим комплексный завод по производству пеллет. Есть два важных фактора такой линии по производству пеллет:
1. Прибыльность. Здесь прибыль может быть показана в двух аспектах. для простых производителей пеллет для домашнего использования они должны убедиться, что общая стоимость производства будет намного ниже, чем стоимость покупки пеллет у других продавцов пеллет. Для владельцев малого бизнеса по производству пеллет, помимо функции экономии, они должны убедиться, что пеллеты, произведенные на производственной линии, пригодны для продажи.
2. Автоматика. Мелкосерийное производство обычно требует производства пеллет постоянного качества с постоянной скоростью. Высокая степень автоматизации производства может значительно сократить затраты на оплату труда и повысить эффективность производства пеллет. На нашей мобильной линии по производству пеллет обычно требуется один оператор, чтобы убедиться, что все в порядке.
Сырье для линии по производству древесных гранул
Эта линия по производству древесных гранул может перерабатывать не только древесную щепу и опилки, но и материалы биомассы, такие как стебли, солома, сено, скорлупа арахиса, шелуха подсолнечника, рисовая шелуха, багасса, скорлупа пальмового ядра и т. д.
Технологическая схема завода по производству древесных гранул Moble
Общие технические параметры 400-600 кг/ч Мобильный завод по производству пеллет
Модель | АМСВПП 400-600кг/ч |
Диаметр древесных гранул | 6–16 мм |
Емкость | 400-600 кг/ч |
Плотность гранул | 1,1-1,4 т/м3 |
Материал Содержание влаги | 13%~18% |
Габаритные размеры (Д*Ш*В) | 8000*2000*3200мм (20 футовый контейнер для доставки) |
Детали завода по производству древесных гранул AMSWPP 400-600 кг/ч
1. Процесс дробления:
Дробилка древесины: первый. Из-за лучшего размера сырья в гранулировании 3-5 мм . Таким образом, на основе различных материалов необходима дробилка для дерева. Наша дробилка для древесины типа 700 является идеальным оборудованием для линии по производству пеллет, которая используется для обработки бревен, квадратных блоков, древесного посоха и т. д. размером менее 200 мм (диаметр). После дробления материала дробилкой для древесины выходной размер может быть диаметром 3-5 мм, что подходит для дальнейшей обработки.
Товар | Количество/единица измерения | Мощность/кВт | Емкость | Вес | Крупногабаритный |
AMS—дробилка для древесины MFS700 | 1 | 22 | 500—750 кг | 1,5 т | 1450x750x950 мм |
2. Система сушки
мгновенная сушка опилок
Наилучшее содержание влаги для гранулирования 12-15% . Поэтому мы предлагаем вам использовать сушилку, если влажность вашего сырья выше 15%. Наша сушилка для опилок TRM—QLHG32 всегда была выбрана клиентами из-за ее высокой эффективности сушки, меньших капиталовложений, чем сушилки других типов, и небольшой общей площади.
Пункт | Количество/единица измерения | Мощность/кВт | Длина/м | Вес/т |
TRM—QLHG32 Мгновенная сушка опилок | 1 | 5,5 | 32 | 1,2 |
3. Воздушный затвор
После сушки материал следует транспортировать в бункер для хранения; здесь необходим воздушный запорный клапан. Благодаря приоритетным функциям воздушной блокировки и блокировки, наш воздушный шлюзовой клапан может контролировать поток материала из циклона в условиях силы тяжести, давления и вакуума, а также блокировать высокотемпературный газ при транспортировке материала в бункер для хранения.
4. Мусорный контейнер
Два иллюминатора с обеих сторон для контроля и наблюдения; Объем 1,2м³.
Товар | Количество/единица измерения | Вес/т | Негабарит/мм |
Бункер для хранения материалов | 1 | 0,25 | 1000x1000x1200 |
5. Шнековый элеватор
Этот тип шнекового элеватора в основном используется для подъема материалов из складского бункера в питатель на производственной линии.
Характеристики
★. Большая вместимость, высокая скорость, гигиеничность и отсутствие пыли.
★. Размер элеватора может быть настроен в соответствии с вашими требованиями и производительностью.
Товар | Количество/единица измерения | Мощность/кВт | Вес/т | Негабарит/мм |
200 винтовой элеватор | 1 | 1,5 (регулятор скорости) | 0,15 | 3800x160x160 |
6. Система подачи: Шнековый питатель
Мощность подачи можно стабильно регулировать, чтобы обеспечить достаточную подачу материала и избежать избыточного сырья, что гарантирует идеальное рабочее состояние гранулятора.
Товар | Количество/единица измерения | Мощность/кВт | Вес/т | Негабарит/мм |
Шнековый питатель 200 | 1 | 1,5 | 0,06 | 1500x160x160 |
7. Система гранулирования: AMSPLM400 Гранулятор с плоской матрицей
После дробления и сушки сырье может быть помещено в гранулятор для древесных гранул. Гранулятор с плоской матрицей типа AMS 400 используется для обеспечения наилучших результатов при производстве древесных гранул. Этот электрический гранулятор с плоской матрицей имеет конструкцию с роликовым приводом, которая обеспечивает более сильное сжатие материалов, поэтому он может легче перерабатывать материалы твердой древесины в гранулы из биомассы, чем другие грануляторы с приводом от штампа. Есть две основные особенности гранулятора, приводимого в движение вращающимися роликами. Во-первых, эта конструкция может продлить срок службы гранулятора, а во-вторых, сделать древесные гранулы более гладкими и твердыми.
Модель | Объем древесных гранул | Мощность двигателя (кВт) | Вес (кг) | Диаметр гранул (мм) | Материал плоской матрицы и ролика | Размер упаковки (мм) |
АМСПЛМ400 | 400-600 кг/ч | 30 | 630 | 6-16 | Легированная сталь | 1450*800*1600 |
8. Охлаждение древесных гранул и просеивающая машина
Гранулы, поступающие с завода по производству древесных гранул, имеют высокую температуру, а некоторые из них фрагментарны, поэтому перед процессом упаковки нам необходимо за короткое время снизить высокую температуру, чтобы получить гранулы с высоким содержанием, и просеять фрагментарные гранулы для упаковки. . Наша охлаждающая и просеивающая машина сочетает в себе охладитель и сито в одной машине. Он может отделять и собирать пыль и фрагменты для повторного использования, а также одновременно снижать температуру гранул с 80 ~ 90 ℃ до примерно 3 ~ 5 ℃ выше температуры окружающей среды, содержание влаги с 17% ~ 18% до 12% ~ 13%. что хорошо для упаковки и хранения пеллет.
Товар | Количество/единица измерения | Мощность/кВт | Вес/т | Негабарит/мм |
500 Горизонтальная охлаждающая и просеивающая машина | 1 | 1,5 | 0,35 | 1400 x 900 x 1300 |
9. Рукавный фильтр
Рукавный фильтр также называется пылесборником, который может эффективно решить проблемы большего количества источников пыли в процессе производства гранул и обеспечить безопасность и чистоту вашей мастерской. Это первый выбор экологически чистого оборудования, широко используемого в производстве древесных гранул.
Товар | Количество/единица измерения | Мощность/кВт | Вес/т | Негабарит/мм |
Мешочный фильтр | 1 | 4 | 0,2 | 1000 x 1000 x 2200 |
10. Ковшовый элеватор
От охлаждающей и просеивающей машины требуется ковшовый элеватор для вертикального подъема гранул и их выгрузки в бункер упаковочной машины.
Этот тип элеватора не требует большого количества материалов, поэтому он может поднимать порошковые материалы, гранулы и т. д. Он также может поднимать материалы из высокотемпературного материала менее чем на 250 градусов.
Товар | Количество/единица измерения | Мощность/кВт | Вес/т | Негабарит/мм |
25 ковшовый элеватор | 1 | 2,2 | 0,45 | 4000 x 650 x 380 |
11. Автоматическая машина для упаковки пеллет
После охлаждения и просеивания, если древесные гранулы не будут непосредственно поступать в топливный процесс, необходимо использовать машину для упаковки древесины во избежание намокания. Наша автоматическая машина для взвешивания и упаковки может автоматически взвешивать и упаковывать пеллеты с высокой точностью, что повышает эффективность производства, снижает трудоемкость и удовлетворяет потребности в высокой степени автоматизации для полного завода по производству древесных гранул.
Товар | Количество/шт. | Мощность/кВт | Вес/т | Негабарит/мм |
25 автоматическая упаковочная машина | 1 | 2,9 | 1,1 | 2000 x 800 x 2500 |
12. Система управления: Встроенный шкаф управления
◆ Благодаря встроенному шкафу управления производственная линия отличается высокой эффективностью и удобством в эксплуатации.
◆ Компактный шкаф управления с защитой от пыли
◆ Полная автоматизация всей производственной линии
◆ Постоянное качество продукции при высокой производительности
◆ Меньшая потребность в рабочей силе, меньшие временные затраты
Товар | Количество/единица измерения | Вес/т | Негабарит/мм |
Встроенный шкаф управления | 1 | 0,26 | 800x350x1400 |
С новой линией по производству древесных гранул производительностью 400-600 кг/ч вам не нужно беспокоиться о качестве пеллет. Пеллеты, произведенные на этом мобильном заводе, имеют хорошую форму, высокую плотность, гладкую поверхность и более длительное время горения.