П-образный компенсатор, П образный компенсатор
Здравствуйте! При нагревании трубопроводы системы теплоснабжения имеют свойство удлиняться. И то, насколько они увеличатся по длине, будет зависеть от их начальных габаритов, от материала, из которого они изготовлены, и температуры вещества, транспортируемого по трубопроводу. В потенциале изменение линейных размеров трубопроводов может привести к разрушению резьбовых, фланцевых, сварных соединений, повреждению иных элементов. Разумеется, при конструировании трубопроводов учитывается то, что они удлиняются при нагревании и укорачиваются при наступлении низких температур.
Самокомпенсация теплотрасс и дополнительные компенсирующие элементы
Существует в сфере теплоснабжения такое явление, как самокомпенсация. Под этим понимается способность трубопровода самостоятельно, без помощи специальных устройств и приспособлений, компенсировать те изменения размеров, которые происходят в результате теплового воздействия, за счёт упругости металла и геометрической формы. Самокомпенсация возможна только при наличии в трубопроводной системе изгибов либо поворотов. Но не всегда при проектировании и монтаже имеется возможность для создания большого количества таких «естественных» компенсаторных механизмов. В таких случаях актуально подумать над созданием и установкой дополнительных компенсаторов. Они бывают следующих типов:
• П-образные;
• линзовые;
• сальниковые;
• волнистые.
Способы изготовления П-образных компенсаторов
В данной статье мы подробно поговорим о П-образных компенсаторах, которые на сегодняшний день являются самыми распространёнными. Данные изделия, покрытые полиэтиленовыми оболочками, можно применять на технологических трубопроводах всех типов. По сути, они являются одним из методов самокомпенсации — на коротком отрезке создаётся несколько изгибов в виде буквы «П», а затем трубопровод продолжает идти по прямой. Такие П-образные конструкции делаются из цельных изогнутых труб, из отрезков труб или отводов, которые сваривают между собой. То есть изготавливают их из того же самого материала, из той же марки стали, что и трубы.
Экономичней всего гнуть компенсаторы из одной цельной трубы. Но если общая длина изделия составляет более 9 метров, то их следует изготовлять из двух, трёх или семи частей.
• В случае, если компенсатор нужно изготовить из двух составных частей, то шов располагается на так называемом вылете.
• Трёхчастная конструкция предполагает, что гнутую «спинку» изделия будут создавать из цельного куска трубы, а потом к ней приварят два прямых отвода.
• Когда частей предполагается семь, то четыре из них должны быть коленцами, а остальные три — патрубками.
Важно помнить и то, что радиус сгиба отводов при заготовке компенсаторов из прямых частей должен быть равен четырём наружным диаметрам трубы. Это можно выразить следующей несложной формулой: R=4D.
Из скольких бы частей не изготавливался описываемый компенсатор, сварной шов всегда желательно располагать на прямом участке отвода, который будет равен диаметру трубы (но не менее 10 сантиметров). Впрочем, бывают ещё и крутозагнутые отводы, где прямые элементы отсутствуют вовсе — в таком случае можно отойти от вышеуказанного правила.
Достоинства и недостатки рассматриваемых изделий
Компенсаторы данного типа специалисты рекомендуют применять для трубопроводов небольшого диаметра — до 600 миллиметров. Участки в виде больших букв «П» на данных трубопроводах при возникновении каких-либо колебаний эффективно гасят их за счёт изменения своего положения по продольной оси. Это как бы не позволяет колебаниям «продвигаться» по теплотрассе дальше. В трубопроводах, требующих разбора для того, чтобы произвести очистку, П-образные компенсаторы дополнительно снабжают присоединительными деталями на фланцах.
П-образные изделия хороши тем, что они не нуждаются в контроле в период эксплуатации. Это их отличает от изделий сальникового типа, для обслуживания которых нужны специальные камеры ответвлений. Однако для обустройства П-образных компенсаторов требуется некоторое пространство, а в плотно застроенном городе оно находится не всегда.
У рассматриваемых компенсаторов, разумеется, есть не только достоинства, но и недостатки. Самый очевидный из них такой – для изготовления компенсаторов дополнительно расходуются трубы, а они стоят денег. Кроме того, установка данных компенсаторов ведёт к тому, что увеличивается общее сопротивление движению жидкости-теплоносителя. Плюс ко всему такие компенсаторы отличают значительные размеры, и потребность в специальных опорах.
Расчёты для П-образных компенсаторов
В России по-прежнему не стандартизированы параметры для П-образных компенсаторов. Их производят в соответствии с нуждами проекта и по тем данным, которые в этом проекте прописываются (тип, размеры, диаметр, материал и т. д.). Но всё-таки определять габариты П-образного компенсатора наобум, конечно, не следует. Специальные расчёты помогут узнать те габариты компенсатора, которые окажутся достаточными для компенсации деформаций теплотрассы из-за температурных перепадов.
При подобных расчётах, как правило, принимаются следующие условия:
• трубопровод изготовлен из стальных труб;
• по нему течёт вода либо пар;
• давление внутри трубопровода не превышает 16 бар;
• температура рабочей среды не более 2000 градусов по Цельсию
• компенсаторы симметричны, длина одного плеча строго равна длине второго плеча;
• трубопровод находится в горизонтальном положении;
• на трубопровод не действует давление ветра и прочие нагрузки.
Как мы видим, здесь берутся идеальные условия, что, разумеется, делает конечные цифры весьма условными и приблизительными. Но такие расчёт всё равно позволяют снизить риск повреждений трубопровода при эксплуатации.
И ещё одно важное дополнение. При расчётах изменения трубопровода под воздействием тепла за основу берётся наибольшая температура перемещаемой воды или пара, а температура окружающей среды, наоборот, выставляется минимальная.
Сборка компенсаторов
Собирать компенсаторы необходимо на стенде или на абсолютно ровной твёрдой площадке, на которой удобно будет производить сварочные работы и подгонку. Начиная работы, нужно точно нанести ось будущего П- участка и установить контрольные маячки для элементов компенсатора.
После изготовления компенсаторов нужно также проверить их размеры — отклонение от намеченных линий должно не превышать четырёх миллиметров.
Монтаж П-образных компенсаторов
Место для П-образных компенсаторов обычно выбирается с правой стороны теплопровода (если смотреть от источника тепла к конечному пункту). Если же справа нет необходимого пространства, то возможно (но лишь в качестве исключения) устроить вылет для компенсатора слева, не меняя в целом расчётные габариты. При таком решении с внешней стороны будет находиться обратный трубопровод, и размеры его окажутся чуть больше тех, что требовались согласно предварительным вычислениям.
Пуск теплоносителя всегда создаёт в трубах из металлов значительное напряжение. Чтобы справиться с ним, П-образный компенсатор в процессе монтажа следует растянуть по максимуму – это увеличит его эффективность. Растяжку делают после установки и фиксации опор с обеих сторон от компенсатора. Трубопровод при растяжке в зонах его приваривания к опорам должен оставаться строго неподвижным. П-образные компенсаторы сегодня растягивают при помощи талей, домкратов и прочих подобных приспособлений. Величину предварительной растяжки компенсирующего элемента (или величину его сжатия) следует обязательно указать в паспорте на теплотрассу и проектных документах.
Если планируется расположение П-образных элементов группами на нескольких трубопроводах, идущих параллельно, то растяжку заменяют такой процедурой, как натяжка труб в «холодном» состоянии. Подобный вариант предполагает и особый порядок проведения монтажных процедур. В данном случае компенсатор прежде всего следует установить на опоры и сварить стыки.
Но при этом в одном из стыков должен остаться зазор, который будет соответствовать заданной растяжке П-компенсатора. Для того, чтобы избежать снижения компенсационной способности изделия и предотвратить перекосы, для натяжения следует воспользоваться стыком, который будет находиться от оси симметрии компенсатора на расстоянии от 20 до 40 трубных диаметров.
Установка опор
Особо стоит сказать об установке опор для П-компенсаторов. Их необходимо смонтировать так, чтобы трубопровод перемещался лишь вдоль продольной оси и никак иначе. В таком случае компенсатор примет на себя все возникающие продольные колебания.
Сегодня для одного П-компенсатора необходимо устанавливать не менее трёх качественных опор. Две из них следует располагать под теми участками компенсатора, которые состыкуются с основным трубопроводом (то есть под двумя вертикальными палочками буквы «П»). Допустимо также монтировать опоры на самом трубопроводе поблизости от компенсатора. Причём между краем опоры и сварным стыком должно быть хотя бы на полметра. Ещё одна опора создаётся под спинкой компенсатора (горизонтальной палочкой в букве «П»), как правило, на особой подвеске.
Если теплотрасса имеет уклон, то боковые части П-образных элементов должны располагаться строго по уровню (то бишь уклон должен соблюдаться). В большинстве случаев компенсаторы в виде буквы «П» устанавливаются горизонтально. Если же компенсатор устанавливается в вертикальном положении внизу обязательно должна быть организована соответствующая дренажная система.
Какие данные о компенсаторах нужно занести в паспорт теплотрассы?
По окончании монтажа П-образного компенсатора в паспорт теплопровода вносятся такие сведения:
• технические параметры компенсатора, предприятие-изготовитель и год производства;
• расстояние меж опорами, производимая компенсация и величина растяжения;
• температура окружающей атмосферы в период, когда проводились работы, и дата установки.
Что касается, например, компенсирующей способности П-образного изделия, то она имеет чёткую зависимость от ширины, от радиуса изгибов и вылета.
teplosniks.ru
Технология монтажа потолка из гипсокартона от простого к сложному
Для воплощения в жизнь самых смелых своих проектов по оформлению потолка, дизайнеры используют гипсокартон. При технологии монтажа потолков из гипсокартона, необходимо создание центральной плоской поверхности, которая позволяет работать со сложными элементами декора. При этом конструкция отличается особой прочностью и надежностью.
Самой простой установкой подвесного потолка, является монтаж потолка с одним или двумя уровнями. Техника создания гипсокартонового потолка из двух уровней будет рассмотрена чуть позже. А вот ознакомиться с некоторыми тонкостями установки одноуровневого потолка из гипсокартона можно в материале «Потолок из гипсокартона своими руками на кухне: особенности монтажа».
Разметка креплений на потолке
Согласно технологии монтажа подвесного гипсокартонового потолка, первое, что необходимо сделать – нанести разметку:
- Так, на стены наносят идеально ровную горизонтальную линию, которая станет чертой потолочного уровня. Для этого используют длинный строительный уровень или водный уровень (ватерпас). Наиболее приемлемая длина уровня составляет полтора-два метра, при этом у него должно быть четыре полоски в смотровом окошке – две с одной стороны от пузырька воздуха и две с другой стороны. При соблюдении данных требований к инструменту, точность разметки гарантирована.
- При завершении очерчивания линии, ее конец должен сойтись с ее началом, при этом малейший ее сдвиг не допустим. При нанесении разметки в углу помещения при помощи строительного уровня, следует придерживаться правил работы с гидроуровнем. Для этого, когда метки наносятся на смежные стены, уровень следует размещать как на поверхности этих стен, так и в углах распор.
Схема технологии при монтаже гипсокартонового потолка
Рекомендация! Для создания качественной разметки потолочного уровня, наиболее оптимальным решением станет использование лазерного уровня.
- После завершения создания горизонтального уровня потолка, следующим шагом станет разметка потолка с местами креплений прямых подвесов. В итоге, на потолке должна появиться сетка с габаритами ячеек 600 х 600 мм. Очень часто, в краях комнаты, размеры ячейки не соответствуют заданным 600 мм, в таком случае следует уменьшить их габариты и сделать симметричными относительно противоположных сторон.
Монтаж профилей для крепления гиспокартона
Монтаж направляющего профиля
Следующий этап монтажа потолка из гипсокартона предусматривает обшивку всего периметра комнаты направляющими профилями (ПН). Размер такого профиля – 2,7 х 2,7 см. Конечно, в этом процессе существую свои особенности:
- Места, где ПН сходится со стенкой, профиль дополнительно проклеивается. Для этого используют уплотнительную ленту, к примеру, фирмы Dichtungsband
- Направляющий профиль имеет стандарт длины три метра. Крепить такие длинные элементы, необходимо не менее, чем в четырех точках соприкосновения со стеной.
- Крепится направляющий профиль при помощи дюбель-гвоздей с грибовидной шляпкой, похожей на шайбу. Благодаря тому, что такое крепление создает усиленный контакт профиля со стенкой, данное соединение будет отличаться своей надежностью и долговечностью.
- При монтаже дюбель-гвоздей следует придерживаться традиционного способа – сначала дюбель вворачивается, а затем, в него устанавливается шуруп.
- При монтаже направляющих профилей, категорически не приемлемо наличие промежутков.
Установка П-образных подвесов
Монтаж подвесов П-образной формы, проводится по заранее намеченной разметке на черновом потолке. При этом интервал должен быть в пределах 70-100 см., а расстояние от стены до подвеса на противоположных стенах должно быть одинаковым.
Для закрепления подвесов не стоит пользоваться дюбель-гвоздями для вертикального крепежа. Рекомендуется использовать дюбеля из пластика и шурупы. Если черновой потолок сделан из бетона, оптимальным решением станут металлические дюбеля, предназначенные для тяжелых конструкций. Однако следует быть внимательным, поскольку рамные дюбеля, тоже металлические, но они совершенно не подойдут для данной цели.
На стыках направляющих профилей, следует установить П-образные подвесы по обе стороны от стыка.
Элементы крепления каркаса гипсокартонной конструкции к потолку
По окончании процесса крепления профилей П-образной формы, следующим этапом является монтаж потолочных профилей (ПП). Их параметры составляют – 5,6 х 2,7 см., иногда встречаются размеры 6 х 2,7 см.
Установка потолочных профилей
Первое, что необходимо сделать при монтаже потолочных профилей – закрепить длинные профили на потолке от стены до стены. Затем установить между ними короткие поперечные профили. При этом крестовые соединения выполняются при помощи специального крепления.
ПП монтируют от стенки и вставляют в направляющие профили. Затем обозначают горизонтальный уровень расположения потолочных профилей (для этой цели используют уровень), а потом крепят его при помощи двухстороннего соединения к П-образному подвесу. При этом для подобного соединения используют шурупы металл-металл (саморезы).
Рекомендация! Для соблюдения правил монтажа потолков из гипсокартона, установку ПП следует контролировать с помощью уровня на протяжении всех проводимых работ.
Чтобы сделать работу более легкой, можно воспользоваться следующими советами:
- Наиболее удобным для монтажных работ станет строительный уровень с одной магнитной стороной;
- Для стыковки профилей можно использовать специальные соединители. Однако данный факт не отменяет применение дополнительных П-образных подвесов;
- Для придания стыку профилей дополнительной прочности, необходимо заранее смонтировать подвес П-образной формы с лева и с право от него.
Наиболее рациональным решением, станет монтаж самых длинных профилей параллельно стенке с окном. Таким образом можно отвлечь внимание от мелких дефектов на месте соединения листов гипсокартона, которые будут крепиться по направлению естественного света из окна.
Крепление гипсокартона на каркасе
Цельный лист гипсокартона (ГКЛ) крепится поперечно длинным направляющим профилям.
Листы соединяют в центральной части профиля. Для качественного монтажа ГКЛ на профиля, рекомендуется работать с напарником. Для прикрепления листов к профилю используют саморезы, при этом шуруп слегка «утапливают» в листе гипсокартона, где-то на два-три миллиметра. Расстояние между саморезами должно быть приблизительно 250-300 мм., а от углов гипсокартона – 30-40 мм.
Помимо этого, шурупы следует начинать крепить не ближе, чем 10-15мм от края гипсокартона. При ввинчивании саморезов, следует быть крайне осторожными и не допустить скола края листа. Однако если такая неприятность все же случилась, необходимо извлечь шуруп и вкрутить новый на расстоянии 30-40 мм от места скола.
При креплении листов гипсокартона к потолку необходимо помнить о следующих нюансах:
- При установке листов гипсокартона следует помнить, что по углам помещения находится узкий профиль, а это может усложнить процесс монтажа;
- Для красивого эстетичного вида гипсокартонного потолка следует придерживаться простого правила: меньше граней – красивее вид;
- В процессе ввинчивания саморезов, следует придерживаться одинаковой глубины «утопления» во всех точках крепления. Такая точность пригодится позже, на стадии проведения малярных работ, она позволит провести их максимально качественно;
- Во избежание возникновения неприятных ситуаций, таких как перепад высот в местах соединения листов, наилучшим вариантом станет использование продукции от одного производителя (к примеру, Knauf).
Технология резки гипсокартонных листов и малярные работы
Для осуществления разметки листов гипсокартона используется алюминиевое правило, которое следует тщательно очистить от всевозможных загрязнений. Если такой инструмент отсутствует, можно воспользоваться ровной рейкой.
- На листе производится разметка, по ней гипсокартон будет обрезаться.
- Далее, делается надрез глубиной 2-4 мм по правилу (или рейке). Для этого используют острый строительный нож, чтобы линия была ровной и не прерывалась.
- После чего, лист гипсокартона кладется на край стола и с помощью осторожного, но уверенного движения ломается. При правильно сделанном надрезе, гипсокартонный лист сломается ровно.
Инструкция по резке гипсокартона
- На тыльной стороне листа останется картон, его можно срезать с помощью строительного ножа.
- Для выравнивания края среза можно использовать рубанок либо наждачную бумагу №4 или №6.
Для покраски гипсокартонного потолка (для ознакомлением с правилами проведения малярных работ читайте: Как покрасить потолок на кухне: выбор краски и порядок работы) необходимо пользоваться малярным бинтом и малярной сеткой, которые используют для проклеивания мест соединений гипсокартона со стенкой и стыков.
Процесс разметки потолка для размещения точечных светильников следует выполнять перед последним нанесением краски. Такой порядок действий позволит предотвратить появление пятен и поможет сохранить видимость меткам для точек освещения. Нанесение последнего слоя краски производится по направлению к самому сильному потоку света.
Рекомендация! Если помещение имеет два и более окна, финальное нанесение краски на гипсокартонный потолок следует производить перпендикулярно самому освещенному окну.
Технология: для покраски подвесного потолка из гипсокартона оптимальным решением будет использование валика, это сэкономит краску и позволит создать равномерное покрытие
Приведенные выше правила технологии создания подвесных потолков из гипсокартона, позволит провести качественный монтаж собственными силами. Однако этого можно достичь только в том случае, если четко соблюдать все инструкции и рекомендации. В противном случае, вы рискуете получить на выходе кривой и ненадежный потолок, который необходимо будет переделывать.
www.potolokguru.com
Монтаж распределительного щитка ЩРН-П
После покупки шкафа ЩРН-П фирмы IEK необходимо его собрать, смонтировать на стену и потом наполнить модульными устройствами (УЗО, автоматическими выключателями и т.д.). Ниже представлена небольшая, но подробная инструкция по монтажу распределительного щитка на примере корпуса ЩРПН-П-12. Она также подойдет и для других типоразмеров шкафов данного производителя.
Монтаж распределительного щитка ЩРН-П
Пластиковый модульный корпус продается в коробке, на которой указана вся необходимая информация об этом изделии.
Открываем коробку и достаем сам корпус…
Для монтажа шкафа на стену, установки шин «N» и «PE», наполнения его автоматическими выключателями и для подключения проводов необходимо снять переднюю панель. Для этого крестообразной отверткой откручиваем два болта, находящиеся под крышкой.
Внутри уже установлена DIN-рейка для установки модульных устройств. В комплекте идут дюбеля с саморезами для крепления основания на стену. Также в пакетике есть шины «N» и «PE», которые необходимо закрепить на черной планке.
Черная планка с шинами крепится в основании шкафа в пазы снизу или сверху.
Перед креплением на стену ЩРН-П-12 продумайте как будут заходить в него подходящие и отходящие провода. В основании корпуса есть разметка отверстий для ввода проводников. Они находятся сверху, снизу и на задней стенке основания. Аккуратно острым ножом вырежьте необходимые отверстия.
Затем на стене разметьте места для сверления отверстий под дюбеля. Для ЩРН-П-12 их два — в центре сверху и снизу. Сверлим отверстия победитовым сверлом диаметром 6 мм, вставляем в них дюбеля, идущие в комплекте, прикладываем основание шкафа к стене и крепим его двумя саморезами.
Остается только установить автоматы и другую модульную аппаратуру, выполнить все внутренние электрические соединения согласно однофазной схемы распределительного щита, подключить подходящие и отходящие провода.
Должно получиться как-то так или на подобие…
Или так…
Также вам может будет интересно прочитать статьи:
Обзор пластиковых щитков ЩРН-П и ЩРВ-П от фирмы IEK
Как собрать распределительный щит?
Однофазная схема распределительного щита — 5 разных вариантов
Трехфазная схема распределительного щита — 5 вариантов
Не забываем улыбаться:
Каждому с детства известно: вещь, обмотанная синей изолентой, будет служить вечно.
sam-sebe-electric.ru
Технологический трубопровод : П-образные компенсаторы
П-образные компенсаторы, как правило, устанавливают в горизонтальном положении или, если это предусмотрено проектом, вертикально, или наклонно. При установке таких компенсаторов вертикально или наклонно в нижних точках с обеих сторон компенсатора размещают дренажные штуцера для отвода конденсата, а в верхней части — воздухоотводчики.
П-образные компенсаторы с предварительной растяжкой монтируют таким образом. На компенсаторе параллельно его спинке устанавливают приспособление для растяжки, состоящее из двух полухомутов, между которыми установлены винт и распорка с натяжной гайкой.
Перед растяжкой замеряют длину компенсатора в свободном состоянии, а затем вращением гайки разводят его на требуемую величину предварительной растяжки. Затем к компенсатору с одной стороны приваривают участок трубопроводов. После этого компенсатор с участком трубопровода поднимают. При подъеме компенсаторы стропят в трех точках, исключая строповку за приспособление.
Для обеспечения нормальной работы компенсатор устанавливают не менее чем на трех подвижных опорах. Две опоры располагают на прямых участках трубопровода, присоединяемых к компенсатору (при этом край опоры должен отстоять от сварного стыка не менее чем на 500 мм), третью опору ставят под спинку компенсатора. После сборки и сварки стыка и закрепления участка трубопровода в неподвижной опоре компенсатор отсоединяют от грузоподъемных средств. Далее участок трубопровода подтягивают к стыку и после его сварки закрепляют в неподвижной опоре; в заключение с компенсатора снимают приспособление для растяжки.
В отдельных случаях П-образные компенсаторы с растяжкой монтируют в иной последовательности. Сначала устанавливают участки трубопровода в подвижных опорах, сваривают стык и закрепляют его в одной неподвижной опоре, а затем присоединяют к этому участку компенсатор или растяжку компенсатора производят после подъема.
При групповом расположении П-образных компенсаторов параллельных трубопроводов (один внутри другого) и в некоторых других случаях предварительную растяжку компенсаторов заменяют натяжением трубопровода в холодном состоянии. В этом случае участки трубопровода и П-образный компенсатор устанавливают на опоры и сваривают стыки, но в одном из стыков (сварном или фланцевом) оставляют зазор, равный заданной величине растяжки компенсатора.
Сварной стык, у которого будет произведена растяжка компенсатора, указывают в проекте. Если такого указания нет, то во избежание перекоса и снижения компенсационной способности компенсатора для растяжки следует использовать стык, расположенный на расстоянии не менее 20 DH и не более 40 DH от оси симметрии компенсатора. Для удобства монтажа трубопровода в стык, намеченный для растяжки, вставляют временное кольцо длиной, равной величине растяжки. Кольцо прихватывают электросваркой к обеим кромкам трубопровода. Иногда на концах стыкуемых труб приваривают временные хомуты из уголков. Через отверстия в них пропускают монтажные удлиненные стяжные шпильки и, затягивая гайки, зажимают временное кольцо, установленное между торцами стыка.
Растяжку П-образного компенсатора выполняют после окончания монтажа трубопровода, контроля качества сварных стыков (кроме замыкающего стыка, используемого для натяжения) и закрепления трубопровода в неподвижных опорах. Для натяжения временные кольца удаляют и стягивают стыки затяжкой гаек монтажных удлиненных шпилек. После прихватки стыка хомуты и шпильки удаляют и окончательно его сваривают.
П-образные компенсаторы устанавливают с соблюдением общего уклона трубопровода, указанного в проекте.
montazhpro.ru
Печатный монтаж. Преимущества — Студопедия.Нет
Технология монтажа РЭА.
1. Технологический процесс пайки.
Для получения качественного соединения пайку необходимо производить в следующей последовательности:
1.1 Очистить соединяемые поверхности от окислов и загрязнений
1.2 Покрыть место пайки флюсом дня зашиты поверхности от окисления
1.3 Залудить место соединения металлических поверхностей, то есть покрыть тонким слоем припоя. Луженая поверхность должна быть ровной, блестящей, без наплывов припоя и непролуженных мест. Oт качества лужения зависит качество пайки.
При необходимости закрепить провода и выводы радиодеталей в соответствии с требованиями к формовке и установке деталей и проводов при печатном и объёмном монтаже
1.4 Непосредственное выполнение пайки, как разъёмного соединения. Место пайки необходимо прогреть до температуры на 50 градусов выше, чем температура плавления припоя. Припой должен хорошо растекаться по месту пайки, количество припоя должно быть минимальным. Пайка должна быть ровной, глянцевой, без пор и посторонних вкраплений. Пайка должна быть «скелетной», то сеть под припоем должен быть виден контур соединяемых выводов или проводов. Должна быть полностью исключена возможность получения «ложной» пайки, при которой существует видимость пайки, но отсутствует электрический контакт. Такие пайки получаются в результате некачественной подготовки поверхностей.
2. Требования к пайке проводов и радиоэлементов.
Провода должны быть залужены и закреплены в соответствии с технологической документацией, но так, чтобы расстояние от изоляции до пайки было 0,5 – 2 мм. Выводы элементов должны быть залужены и отформованы. Детали устанавливают в соответствии со сборочным чертежом. Высота выводов над поверхностью платы должна быть в пределах 0,5 – 2 мм. Затем выполняют пайку.
Место пайки необходимо прогреть до температуры на 50 градусов выше, чем температура плавления припоя. Припой должен хорошо растекаться по месту пайки, количество припоя должно быть минимальным. Пайка должна быть ровной, глянцевой, без пор и посторонних вкраплений. Пайка должна быть «скелетной», то есть под припоем должен быть виден контур соединяемых выводов или проводов. Должна быть полностью исключена возможность получения «ложной» пайки, при которой существует видимость пайки, но отсутствует электрический контакт. Такие пайки получаются в результате некачественной подготовки поверхностей.
3. Подготовка паяльника к работе.
При пайке радиоэлектронной аппаратуры применяются паяльники мощностью 40 ватт и меньше. Рабочее напряжение паяльника должно быть не более 42 вольт. Изоляция соединительного шнура и вилка должны быть без повреждений. Жало паяльника должно быть неподвижно закреплено.
Для качественного выполнения монтажа необходимо следить, чтобы на жале паяльника не образовывались раковины и сколы. Рабочая поверхность жала всегда должна быть ровная и блестящая, при наличии неровностей жало паяльника обрабатывают и затачивают напильником под углом 45о— 60о . Нагар, образующийся в процессе выгорания канифоли, необходимо убирать хлопчатобумажной салфеткой через 3-4 пайки.
Необходимо следить за температурой жала паяльника, которая на 50-60 градусов должна быть выше температуры плавления припоя. При пайке припоем ПОС-61 с температурой плавления 190о жало должно иметь температуру 240о-250о.
Для измерения температуры используют термопару. При ее отсутствии, степень нагрева можно определить визуально: если канифоль очень быстро сгорает на жале паяльника с выделением большого количества дыма и припой скатывается с рабочей части, значит, паяльник перегрет; если припой долго плавиться и в процессе пайки тянется за паяльником, то имеет место недогрев. Температуру можно регулировать, изменяя величину рабочего напряжения.
4. Монтажные провода. Марки. Применение
Изготавливаются из чистой электротехнической меди, применяются при объёмном монтаже для внутриблочных и межблочных соединений. Провода могут быть одножильными и многожильными. Большинство монтажных проводов для обеспечения быстрой и надёжной пайки и для зашиты от окисления выпускают с лужёными токоведущими жилами. Лужение производят припоями ПОС-40. ПОС- 61. для высокочастотных цепей радиоэлектронной аппаратуры лужение может быть выполнено серебром.
Маркировка проводов:
ПMB — провод монтажный в полихлорвиниловой изоляции(одножильный)
МГВ — провод монтажный гибкий в полихлорвиниловой изоляции многожильный)
МГШВ — провод многожильный монтажный в шёлковой виниловой изоляции
МГВЭ — провод монтажный гибкий в полихлорвиниловой изоляции (многожильный) экранированный
МГШВЭ — провод многожильный монтажный в шёлковой виниловой изоляции экранированный
МГТФ — провод монтажный гибкий термостойкий с изоляцией из фторопласта
МГТФЭ — провод монтажный гибкий термостойкий с изоляцией из фторопласта экранированный
МГСТ — провод многожильный термостойкий с изоляцией из стекловолокна
В конструкторской документации обязательно указать ГОСТ или технические условия, в соответствии с которыми изготавливают провод, марку провода, сечение токоведущей жилы, при необходимости – цвет
5. Правила выбора и обработки монтажных проводов.
Сечение токоведущей жилы выбирают в зависимости от величины проходящего по ним тока. Изоляцию провода выбирают в зависимости от величины рабочего напряжения и условий эксплуатации. В условиях нормальной температуры и влажности используют провода с полихлорвиниловой и волокнистой (хлопчатобумажной) изоляций. В условиях повышенной температуры и влажности применяются провода с изоляцией из фторопласта, стекловолокна, резины. Для защиты от внешних электромагнитных полей используются экранированные провода. Экраны изготавливают из тонкой лужёной медной проволоки.
Изоляция монтажных проводов снимается методом электрообжига (электронож или паяльник). Применение кусачек и другого режущего инструмента не допускается во избежание обрыва отдельных проволок. Потемнение и оплавление изоляции при обжиге допускается не более, чем на 1мм. Изоляцию снимают на расстоянии 10-15мм. Жилы многожильных проводов скручивают под углом 15- 30 градусов к оси провода. После скрутки провод залуживают, отступая от изоляции на 1мм. Лужение должно быть «скелетным».
6. Правила крепления проводов к контактам различного типа.
Способ крепления провода зависит от типа контакта:
1. Штыковые контакты. К ним провода сечением 0.35мм и меньше крепят полным оборотом вокруг штыка. Провода большего сечения крепят на три четверти оборота. Крепить провода нужно так, чтобы расстояние от пайки до изоляции провода было 0.5-2мм (I мм). На I штырёк допускается крепить не более трёх проводов, каждый провод закрепляется самостоятельно.
2. Трубчатые контакты пайка производится без механического крепления. Провод заводят в контакт и запаивают так, чтобы расстояние от пайки до изоляции провода было 0.5-2мм
3. Лепестковые контакты. Маломощные контакты (легко гнутся) паяют без механического крепления. Провод заводят в отверстие, плотно зажимают к лепестку и запаивают по всей поверхности соприкосновения.
Мощные контакты. К ним провода припаивают с предварительным механическим креплением. маломощном контакте. На один лепесток крепят не более трёх проводов. Так же необходимо соблюдать основное требование при пайке проводов — расстояние от пайки до изоляции провода должно быть 0.5-2мм.
7. Виды монтажа радиоэлектронной аппаратуры. Их отличия
При изготовлении радиоаппаратуры используются следующие виды монтажа:
1.Объёмный монтаж. Обеспечивает соединения различных электро и радиоэлементов, узлов и модулей радиоэлектронной аппаратуры в единую конструкцию при помощи проводов, жгутов, разъёмов, кабелей и т.д. Элементы устанавливаются на платах со штырьками, микросхемы при объёмном монтаже не применяются.
Недостатки: высокая трудоёмкость, невозможность автоматизации и механизации, трудность получений идент ичных образцов, наличие паразитных ёмкостей и наводок на длинных проводах.
2. Печатный монтаж. Это электрическое соединение радиоэлементов с помощью плоских печатных проводников на плате, которые получают методом металлизации поверхности или травлением фольгированных материалов, плоские
медные проводники заменяют монтажные провода. Печатный монтаж может быть односторонним, двухсторонним и многослойным. Преимущества: уменьшение габаритов и веса изделий. Возможность автоматизации и механизации производства. Устранение паразитных ёмкостей и наводок. Повышение надёжности, получение идентичных образцов.
3. Поверхностный монтаж. Является разновидностью печатного монтажа. Радиоэлементы устанавливаются на поверхности печатной платы, а не в отверстие как при печатном монтаже. Для выполнения поверхностного монтажа требуется специальная элементная база, освоение новых технологических процессов, высокая точность сборочно-монтажных работ. При поверхностном монтаже дополнительно уменьшаются габариты и массы изделия, повышаются технические характеристики.
Объёмный монтаж. Недостатки.
Объёмный монтаж обеспечивает соединения различных электро и радиоэлементов, узлов и модулей радиоэлектронной аппаратуры в единую конструкцию при помощи проводов, жгутов, разъёмов, кабелей и т.д. Элементы устанавливаются на платах со штырьками, микросхемы при объёмном монтаже не применяются. Объёмный монтаж выполняется в следующей последовательности:
· мерная резка провода
· удаление изоляции с жил монтажных проводов
· заделка концов волокнистой изоляции или экранирующей оплётки при помощи нитяного бандажа, клея или изоляционной трубки
· скрутка и лужение токоведущей жилы
При выполнении объёмного монтажа необходимо соблюдать ряд требований:
· все соединения проводов должны выполняться только после механического крепления,
· не допускается повреждение изоляции провода
· монтажные провода должны иметь запас на 1,2 перепайки
· если расстояние между токоведущими контактами менее 2мм. то на выводы надевают изоляционную трубку
· расстояние между проводами и подвижными частями изделия должно быть не менее 5 мм.
Недостатки: высокая трудоёмкость, невозможность автоматизации и механизации, трудность получений идентичных образцов, наличие паразитных ёмкостей и наводок на длинных проводах.
Печатный монтаж. Преимущества
Печатный монтаж — это электрическое соединение радиоэлементов с помощью плоских печатных проводников на плате, которые получают методом металлизации поверхности или травлением фольгированных материалов, плоские медные проводники заменяют монтажные провода. Печатный монтаж может быть односторонним, двухсторонним и многослойным.
Печатный монтаж выполняют в следующей последовательности:
· Осуществляется входной контроль печатной платы и радиоэлементов
· Производится формовка и установка радиоэлементов на плату в соответствии со сборочным чертежом.
· Производится пайка
Преимущества: уменьшение габаритов и веса изделий. Возможность автоматизации и механизации производства. Устранение паразитных ёмкостей и наводок. Повышение надёжности, получение идентичных образцов.
Двухсторонний и многослойный печатный монтаж позволяет дополнительно уменьшить габариты и вес изделия.
studopedia.net
инструкция по монтажу своими руками, видео и фото
Гиспокартон является очень востребованным материалом для реализации самых замысловатых дизайнерских решений в оформлении потолка. Технология монтажа потолка из гипсокартона основывается на создании базовой плоской поверхности. С ее помощью облегчается работа со сложными элементами композиции, упрощается разметка, а сама конструкция получается более прочной и надежной.
Наиболее прост в монтаже подвесной потолок, состоящий из одного или двух разных по высоте уровней. Технология установки двухуровневых потолков из гипсокартона будет описана ниже. Некоторые тонкости монтажа потолка из гипсокартона можно прочесть в статье – Потолок из гипсокартона своими руками на кухне: особенности монтажа.
Разметка креплений на потолке

Изготовление гипсокартонного потолка
Монтаж потолка из гипсокартона предполагает первым делом нанесение разметки:
- На стены наносится идеально ровная горизонтальная линия, которая является чертой потолочного уровня. При этом используется длинный строительный уровень или гидроуровень (ватерпас). Подходящая длина строительного уровня – около 1,5-2 м, сам он должен иметь 4 риски в смотровом окошке: по 2 с обеих сторон от пузырька воздуха. Такие требования к инструменту позволяют гарантировать точность разметочных мероприятий.
- Получившаяся линия обязательно должна замыкаться, то есть заканчиваться в начальной точке, смещения не допускаются. В углах комнаты разметка строительным уровнем производится аналогично работе с водным уровнем. При нанесении меток на соседние стены уровень размещается не только на поверхности стен, но и в углах в распор.

Потолок из гипсокартона: технология предусматривает следующую схему монтажа
Совет! Самая качественная разметка потолочного уровня получается при использовании лазерного уровня.
- Горизонтальный уровень потолка готов. Далее разметка переносится на потолок, отмечаются места крепления прямых подвесов. Результатом должна стать нанесенная на потолок сетка с ячейками 60 х 60 см. Скорее всего, по краям помещения ячейки не будут равны 60 см, тогда необходимо не только уменьшить их размер, но и сделать симметричными относительно противоположных сторон.
Монтаж профилей для крепления гиспокартона
Монтаж направляющего профиля
По всему периметру комнаты закрепляется направляющий профиль (ПН) размерами 27 х 27 мм.
При этом, однако, существуют определенные нюансы:
- В местах соприкосновения ПН со стеной следует проклеить профиль уплотнительной лентой (например, «Dichtungsband»).
- Стандартная длина ПН – 3 м, при креплении таких длинных элементов, соединение со стеной должно происходить минимум в 4 местах.

Крепление направляющего профиля
- Используемые для крепления дюбель-гвозди должны иметь «грибовидную» шляпку, похожую на шайбу. Такой крепеж создает долговечное и надежное соединение, так как усиливает контакт профилей со стеной.
- Монтаж дюбель-гвоздей лучше проводить классическим способом: вворачивание дюбеля и последующая установка в него шурупа.
- Промежутки между направляющими профилями не допустимы.
Установка П-образных подвесов
Подвесы П-образной формы закрепляются по нанесенной разметке на черновом потолке с интервалом 0,7-1 м. Отступы от противоположных стен должны быть симметричными.
В качестве крепежа не рекомендуется использовать дюбель-гвозди, предназначенные для вертикальных креплений. Лучше взять пластиковые дюбели и шурупы. Для бетонного потолка подойдут дюбели из металла для тяжелых конструкций. Важно не спутать их с рамными, которые также полностью выполняются из металла.
В местах, где стыкуются профили, П-образные подвесы устанавливаются по обеим сторонам стыка.
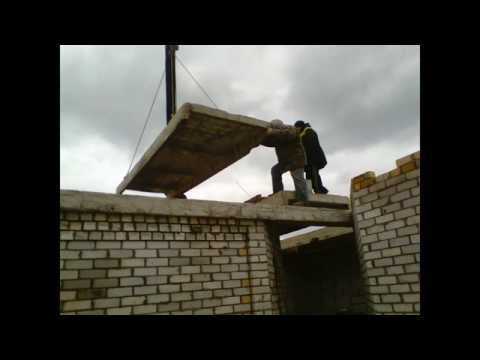
Элементы крепления каркаса гипсокартонной конструкции к потолку
После установки профилей П-образной формы приступают к монтажу потолочных профилей (ПП) с параметрами 56 х 27 мм (60 х 27).
Установка потолочных профилей
Монтаж ПП начинается с закрепления длинных профилей на потолке от одной стены до другой. В промежутках между ними устанавливаются поперечные более короткие профили. Крестовые соединения осуществляются посредством специального крепежа.
Потолочные профили устанавливаются от стены и вставляются в направляющие профили. Далее с помощью уровня обозначается горизонтальный уровень расположения ПП и происходит прикрепление его к П-образному подвесу. Соединение двустороннее, производится шурупами металл-металл (саморезами).
Совет! При монтаже потолочных профилей необходимо постоянно прибегать к помощи строительного уровня. Без него технология установки гипсокартонных потолков будет нарушена.
Для облегчения работы весьма актуальны следующие рекомендации:
- удобно использовать строительный уровень, одна из сторон которого магнитная;
- стыковка профилей может выполняться специальными соединителями, но это не означает, что применение дополнительных подвесов П-образной формы больше не требуется;
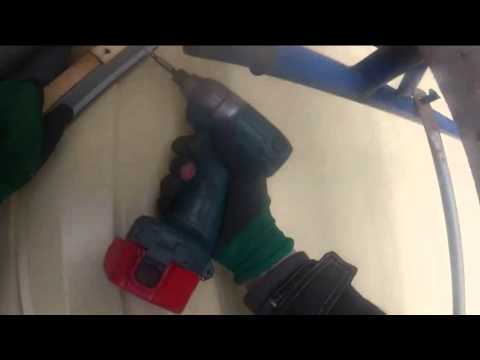
Соединение двух коротких профилей в один
- стык профилей будет прочным, если по обе стороны от него предварительно монтировать П-образный подвес.
Наиболее длинные профили целесообразно закреплять параллельно стене, на которой есть окно. Это отвлечет внимание от несовершенств в местах стыков гипсокартонных листов, так как листы будут монтированы по направлению проникающего из окон дневного света.
Крепление гипсокартона на каркасе
Цельные листы гипсокартона (ГКЛ) крепятся перпендикулярно длинным направляющим профилям.
Стыкование листов осуществляется на середине профиля. Чтобы закрепить ГКЛ на профиле качественно, лучше выполнять эту работу вдвоем. Листы соединяются с профилем саморезами, при этом шурупы нужно немного «утопить» в ГКЛ – буквально на 2-3 мм. Промежуток между креплениями составляет примерно 25-30 см, а от углов гипсокартона – 3-4 см.
Также должен соблюдаться отступ от края ГКЛ до места вворачивания саморезов – 1-1,5 см. Запрещается образование сколов края листа. Если это все же произошло, саморез извлекается и рядом (через 3-4 см от места скола) вворачивается новый.
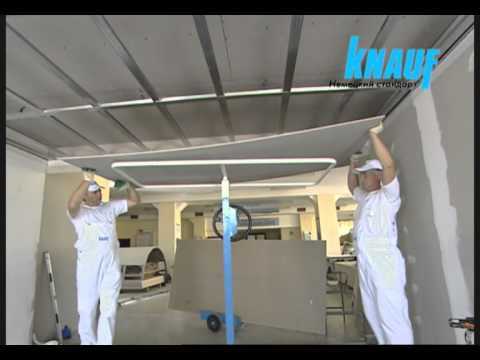
Крепление гипсокартона к профильной системе
Технология монтажа гипсокартона на потолок имеет ряд особенностей:
- в углах комнаты расположен узкий профиль, что усложняет крепление ГКЛ, это нужно учитывать при монтаже; есть простое правило: потолок из гипсокартона тем красивее, чем меньше в нем стыков;
- при вворачивании саморезов в гипсокартон нужно следить за тем, чтобы глубина «утопления» была максимально одинаковой по всей поверхности потолка – это сделает последующие малярные работы более качественными;
- гипсокартонная конструкция в комнате должна состоять из материала одного производителя (например, «Кнауф»), в противном случае возможны перепады высоты в местах стыкования.
Технология резки гипсокартонных листов и малярные работы
Разметка гипсокартонных листов должна осуществляться правилом из алюминия, предварительно очищенным от загрязнений. Если инструмента нет, подойдет ровная рейка.
- На лист наносится разметка, по которой будет происходить резка.
- На глубину 2-4 мм по правилу (или рейке) острым строительным ножом производится надрез. Линия должна быть ровной, непрерывной.
- Лист гипсокартона помещается линией надреза к краю стола и осторожным, но уверенным движением ломается. Если надрез был сделан правильно, ГКЛ сломается ровно.
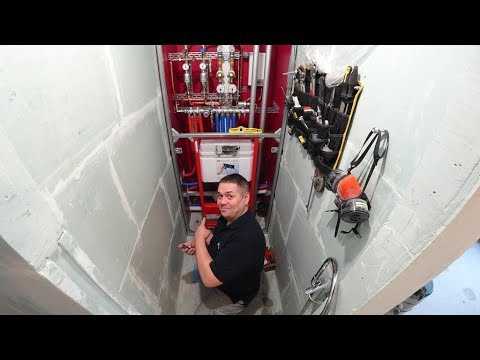
Инструкция по резке гипсокартона
- Картон с обратной стороны листа срезается строительным ножом.
- Края среза выравниваются рубанком или наждачной бумагой № 4 или 6.
При окрашивании гипсокартонной конструкции (о том, как правильно произвести малярные работы см. статью Как покрасить потолок на кухне: выбор краски и порядок работы) обязательно используются малярный бинт и малярная сетка, необходимые для проклеивания стыков и мест соединения ГКЛ со стеной.
Разметка под точечные светильники выполняется перед финальной покраской. Это предотвратит возможные пятна, а также оставит метки под светильники видимыми. Финальное покрытие краской осуществляется по направлению к наиболее сильным потокам света.
Совет! Если в комнате не одно, а два окна, то последнее окрашивание гипсокартонной конструкции на потолке должно производиться перпендикулярно тому окну, которое выходит на солнечную сторону.
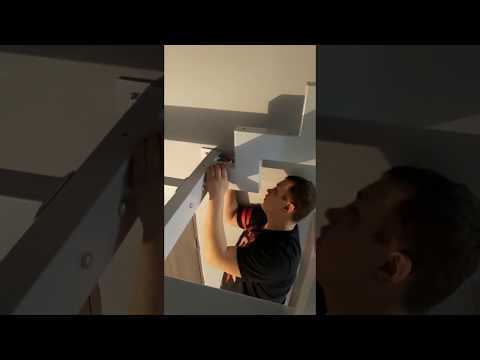
Технология: подвесные потолки из гипсокартона лучше красить валиком с целью экономии краски и создания более равномерного покрытия
Подвесные потолки из гипсокартона технология изготовления которых была описана и проиллюстрирована в данной статье, позволят достичь необходимого результата при условии четкого следования приведенным инструкциям. В ином случае существует риск создания неровного и ненадежного потолка, требующего переделки.
potolokspec.ru
Сэндвич панели-правильная и простая технология монтажа
В настоящее время при возведении объектов самого различного хозяйственного предназначения широкой популярностью пользуются материалы, называемые сэндвич-панелями. Что представляет собой традиционная сэндвич-панель? Сэндвич-панель – это своеобразная плита, имеющий трехслойную структуру. Как правило, два внешних слоя этой плиты являются жесткими материалами, а прослойка между ними представляет собой утеплитель.
Сэндвич-панели характеризуются превосходными свойствами звуко- и теплоизоляции, они обладают высокой устойчивостью к возгоранию, создают надежный барьер для проникновения влаги, обладают высокими антикоррозийными характеристиками, просты в монтаже и не требуют в ходе последующей эксплуатации дорогостоящего ухода. Строения на основе сэндвич панелей возводятся в кратчайшие сроки. Все эти характеристики обеспечивают материалу всеобщую востребованность.
Технология монтажа конструкций на основе сэндвич-панелей проста и максимально доступна. Она не требует применения каких-либо особенных строительных навыков и использования сложных строительных приспособлений или специализированного инструмента. Однако, для того чтобы здание на основе этого материала служило своим хозяевам верой и правдой в течение достаточно продолжительного времени, исчисляемого десятками лет, необходимо неукоснительно выполнять все тонкости технологии монтажа сэндвич-панелей.
Что необходимо выполнить до начала монтажа?
Перед тем как приступить к выполнению монтажных работ, необходимо самым внимательным образом изучить проектную и монтажную документацию. Как правило, подобная документация содержит исчерпывающую информацию о функциональном предназначении панелей (кровельные, стеновые и т.п.), а также способах их монтажа. Кроме этих данных, техническая документация содержит сведения о технических характеристиках материала. Здесь указан тип панелей, размеры панелей, разновидность профиля, варианты крепления к опорным конструкциям, а также сертификаты качества и соответствия тем или иным стандартам.
В технической документации указан рекомендуемый тип и количество соединительных элементов в узлах крепления и местах примыкания. Также должны быть приведены спецификации архитектурных, фасонных и отделочных элементов. Подобная информация представлена в виде чертежей. Кроме прочего, техническая документация должна содержать информацию о количестве необходимых материалов для обустройства надежной гидро- и теплоизоляции.
И, конечно же, техническая документация должна содержать в себе схемы монтажа отдельных сэндвич-панелей, рекомендации по их установке, а также меры безопасности, которые необходимо организовать и выполнять в ходе выполнения монтажных работ.
Ключевые моменты при выполнении монтажных работ
Для достижения высокого качества в ходе выполнения монтажных работ следует уделить повышенное внимание выполнению следующих требований:
— Перед началом монтажных работ следует убрать с территории стройплощадки имеющийся на ней строительный мусор, а также прочие предметы, которые не будут востребованы при монтаже. Площадь строительной площадки необходимо выровнять.
— Перед началом монтажа необходимо осмотреть используемые панели на предмет отсутствия на их поверхности повреждений и коррозии. Также, необходимо осмотреть металлический каркас, на котором будут установлены панели. Он тоже должен быть лишен указанных выше повреждений. Если для монтажа используется каркас из дерева, его необходимо обработать специальным антисептическим составом, предохраняющим древесину от гниения. Для защиты дерева от повреждений насекомых его поверхность покрывают инсектицидами.
— Проверьте размеры используемых панелей на предмет соответствия данных, приведенных в спецификации.
— Используйте доборные элементы, изготовленные тем же производителем, который является изготовителем панелей.
— В случае возникновения необходимости разрезания панелей необходимо использовать только дисковую пилу по металлу или электрический лобзик. Использование для резки сэндвич-панелей любой разновидности газопламенной аппаратуры категорически запрещается!
— Используемое оборудование следует закреплять к дополнительным подвесным конструкциям, но не к монтируемым панелям.
— С целью очистки поверхности сэндвич-панелей от различного рода загрязнений не следует использовать щелочи, кислоты, а также абразивные вещества.
— Запрещается снимать защитную пленку с поверхности материала как при очень низкой, так и при очень высокой температуре окружающей среды. На поверхность пленки не должны попадать прямые солнечные лучи. Пленка не должна быть подвержена воздействию растворителей. Защитную пленку с поверхности сэндвич-панелей разрешается снять только по истечении 10 дней с момента завершения монтажных работ.
— Запрещается размещать на поверхности панели какие-либо посторонние предметы, так как они могут повредить антикоррозийное защитное покрытие на основе полимеров.
— Запрещается перемещение людей и передвижение прочих объектов по поверхности сэндвич-панелей.
Особенности подъема панелей на высоту
Для подъема панелей на высоту следует использовать вакуумные подъемники. В том случае, если подъем транспортного пакета будет осуществляться с применением грузоподъемного крана, необходимо использовать исключительно мягкие стропы в совокупности с деревянными брусками-распорками, имеющими длину не менее 1,2 метра. Подобные распорки выполняют функцию защиты замковых элементов панелей от вероятного повреждения при соприкосновении со стропами.
Используемые бруски необходимо располагать равномерно под и над транспортируемым пакетом. Ни в коем случае не следует допускать возможности захвата стропами тела самого пакета. Чтобы исключить деформацию замковых элементов, не разрешается стыковать под углом отдельные панели, а также поднимать их непосредственно с паллеты. Отдельные панели необходимо стыковать между собой только в вертикальном положении. Монтажные работы необходимо выполнять с максимальной осторожностью, не допуская повреждений покрытия. Не забывайте, что в случае повреждения покрытия значительно ухудшаются антикоррозийные характеристики материала, а также снижается продолжительность его срока службы.
Разрезание панелей
Перед началом операции, связанной с резкой панелей, необходимо с помощью строительного уровня проверить соответствие линий разметки строго горизонтальному положению. После того как соответствующая проверка горизонтальности выполнена, и ее результат можно считать удовлетворительным, специалист должен приступить к процессу разрезания. В первую очередь следует разрезать металлический слой, в след за ним – слой утеплителя.
Необходимо учитывать, что покрытие сэндвич-панелей достаточно своеобразно реагирует на любые повышения температуры. В случае перегрева, поверхность металлического листа теряет свою способность противостоять губительному воздействию коррозии. В этой связи использовать плазменную резку и шлифовальные машины при резке панелей категорически запрещается.
В том случае, если объем разрезаемого материала невелик, допускается использование электрических ножниц по металлу. В этом случае посредством электрических ножниц металлическая обшивка панелей разрезается по отдельности. По окончании каждой операции, связанной с разрезанием или сверлением материла, необходимо тщательным образом убирать с его поверхности образовавшуюся стружку. Также, от стружки следует очищать поверхность замков панелей. Выполнять маркировку поверхности панелей допускается исключительно маркером или прочими незаостренными предметами.
Варианты крепления панелей
Так как опорные конструкции могут быть изготовлены на основе самых разнообразных материалов, крепления панелей необходимо выбирать исходя из особенностей конструкции, ее толщины и типа. Наиболее распространено крепление посредством саморезов. Для выбора длины саморезов учитывают толщину каркаса, толщину тела панели, величину бура самореза, после чего к полученной сумме добавляют дополнительно 5 мм, компенсирующих толщину используемой шайбы. Для того чтобы не повредить поверхность панели, используют исключительно резиновые шайбы под саморезы. Использование резиновых шайб исключает вероятность повреждения покрытия панели головкой металлического самореза в ходе вкручивания, а также обеспечивает высокую герметичность в местах соединений. Доборные элементы закрепляют посредством специально предназначенных для этой цели заклепок или же саморезами небольшой длины.
В случае использования для закрутки саморезов шуруповерта, необходимо отрегулировать величину момента затяжки. Это исключит вероятность деформирования и последующего выхода из строя резиновой шайбы. Вкручиваемый саморез должен проникать в тело панели только под углом 90°, он не должен деформировать шайбу или прижимать ее к телу панели слишком сильно.
Для того чтобы осуществить правильный расчет количества саморезов, необходимо принимать во внимание особенности расположения панели, тип объекта и ветровую нагрузку на его поверхности.
Как правило, панели, имеющие длину свыше 6 метров, крепят посредством 8 шурупов. Для крепления панели длиной 6 метров потребуется 6 шурупов. Панель длиной 4 метра крепят 4-я шурупами.
Требования к несущей конструкции
Длину пролетов, расположенных между соседними местами крепления сэндвич-панелей, необходимо рассчитывать с учетом собственной толщины панелей. К примеру, если ветровая нагрузка составляет 45 кг/м, для панелей, имеющих толщину 150 мм, величина длины пролет не должна превышать 7 метров. Таким образом, для панелей с толщиной 120 мм – 6, 25м, 100 мм – 6 м, 80 мм – 5 м, 50 мм – 4 м.
Самым лучшим вариантом считается система крепления в один пролет. Однако, это возможно только в тех случаях, когда позволяет длина самого пролета. Конструкции подобного рода характеризуются высокой степенью надежности. В том случае, когда ветровая нагрузка превышает указанные выше величины, следует устанавливать дополнительные крепежные элементы.
Порядок выполнения монтажных работ
Последовательность выполнения монтажных работ полностью зависит от вида конструкции, является она вертикальной или горизонтальной. В случае вертикальной конструкции, монтаж начинают со стороны угла, от той панели, которая будет первой со стороны стыка. Если конструкция горизонтальная, монтаж необходимо начинать с цокольного ряда, после его завершения нужно переходить к следующему ряду. Комбинировать последовательность, регламентируемую этими методами, комбинировать нельзя, так как можно столкнуться с ситуацией, при которой возникнет отклонение в размерах. Монтаж вертикального или горизонтального ряда заканчивается, при необходимости, доборной панелью. Размеры этой панели подгоняют по месту в ходе разрезания.
Чтобы исключить прямой контакт панели с конструктивными элементами опор, применяют уплотнитель. В качестве уплотнителя используют минеральную вату, монтажную пену, силиконовый герметик или полимерную ленту. Технологический шов при длине панелей менее 4 метров должен иметь длину 1,5 см, для панелей большего размера величина этого показателя должна быть менее 1 см.
При выполнении вертикального монтажа замковые части конструкции необходимо стыковать более плотно.
Панели должны иметь непосредственный контакт с поверхностью утеплителя. С этой целью их прижимают к поверхности утеплителя, используя умеренную силу зажима, дабы избежать их повреждений. Горизонтальный монтаж более прост в исполнении, при его реализации замковые части без проблем стыкуются друг с другом в результате собственного веса. Для герметизации соединений применяют силиконовый герметик, обеспечивая условия отсутствия вероятности вступления герметика с покрытием панели в химическую реакцию.
Для защиты примыканий от воздействий внешнего характера используют доборные элементы в качестве деталей, укрывающих щели. Эти фасонные детали крепят в необходимых местах, обрабатывая их внутреннюю поверхность герметиком. С целью надежного закрепления доборных элементов применяют саморезы и заклепки, устанавливаемые с шагом 300 мм. Заводскую пленку с поверхности доборных элементов снимают до начала выполнения монтажных работ.
Постройка каркасного дома своими руками, этапы Строительство быстровозводимых домов из металлических сэндвич панелей Мокрый фасад-технология монтажа
superarch.ru